Two restorations in Bridgeport, Conn., benefitted from a new dustproofer for interior brick without leaving a shine.
Not everyone saw the potential in two completely run-down former factories in Bridgeport, Conn., a town situated at the mouth of the Pequonnock River on Long Island Sound, about 60 miles northeast of Manhattan.
Many developers would have taken one look at the decrepit masonry, all the broken glass and the requirements to remediate and remove hazardous materials, and opted to tear all of it down to build something from scratch.
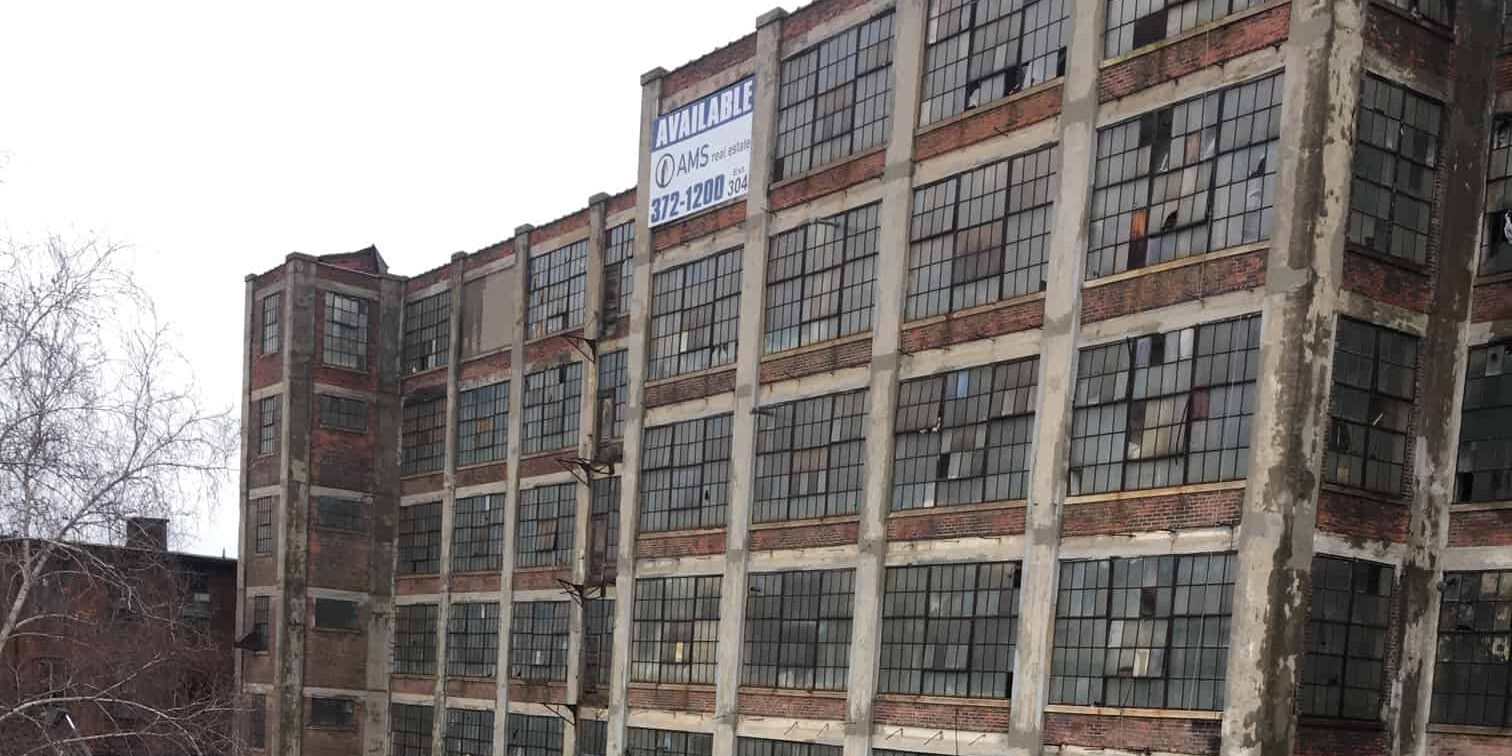
But the long-abandoned buildings at 375 Howard Avenue and nearby Cherry Street, whose historical industrial purposes “involved the extensive use of oils, solvents, acids and metals,” held promise for Gary Flocco, managing partner for Corvus Capital, an international investment firm.
His firm seemed particularly well-positioned to adapt the properties into updated, upcycled uses – they had experience with brownfield (land or property requiring remediation) projects in the past, and on ones involving historic tax credits. As someone who takes pride in seeing potential where others don’t, Flocco and his partners were ready to take it on.
Adapting structures to meet modern needs
Bridgeport is not unlike other cities across New England and the U.S. Over several decades in the 20th century, industrial demand vanished and businesses shut down. But the remnants remained in the form of old factories and warehouses just sitting there, suffering from atrophy and causing blight to communities.
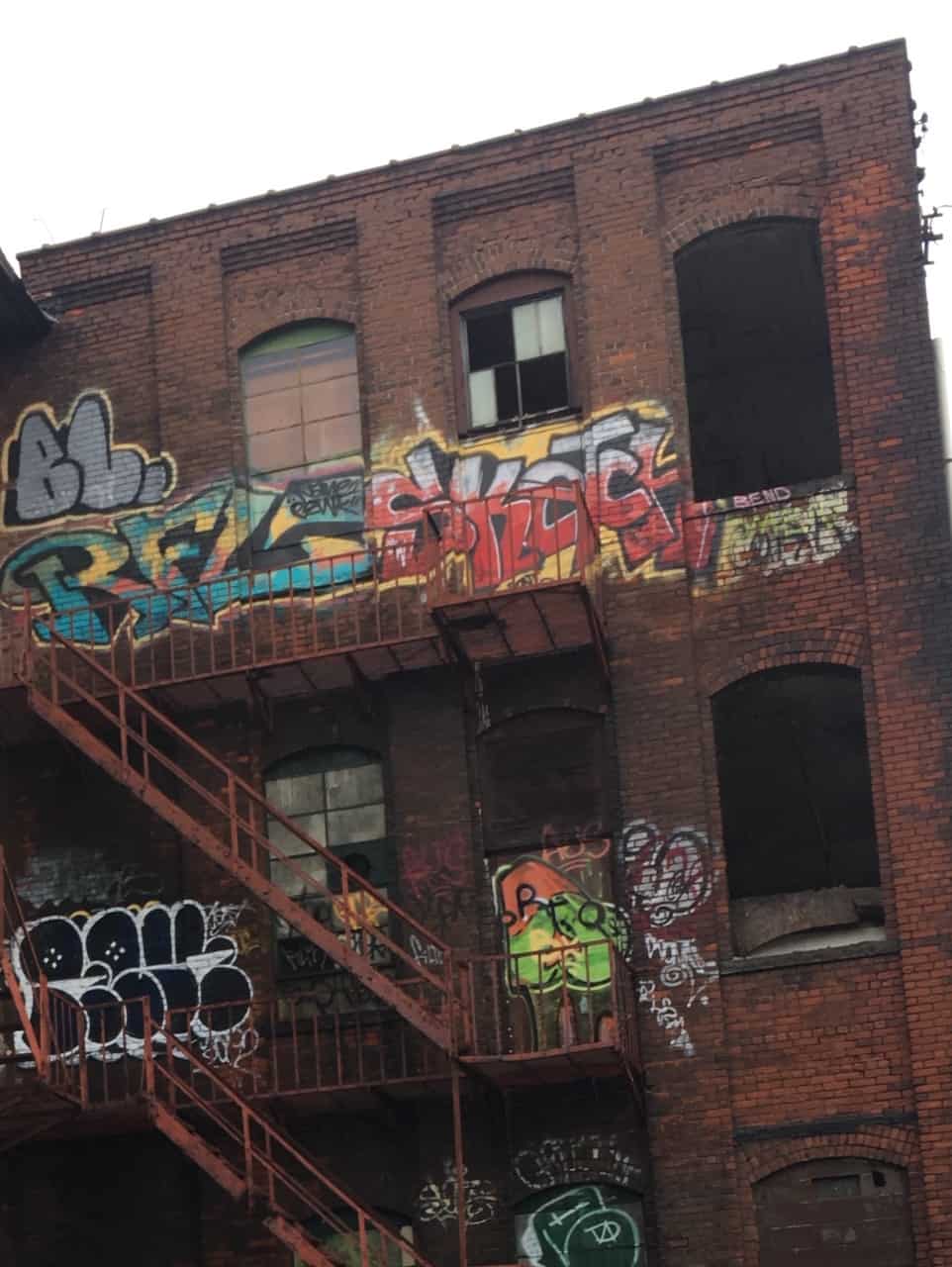
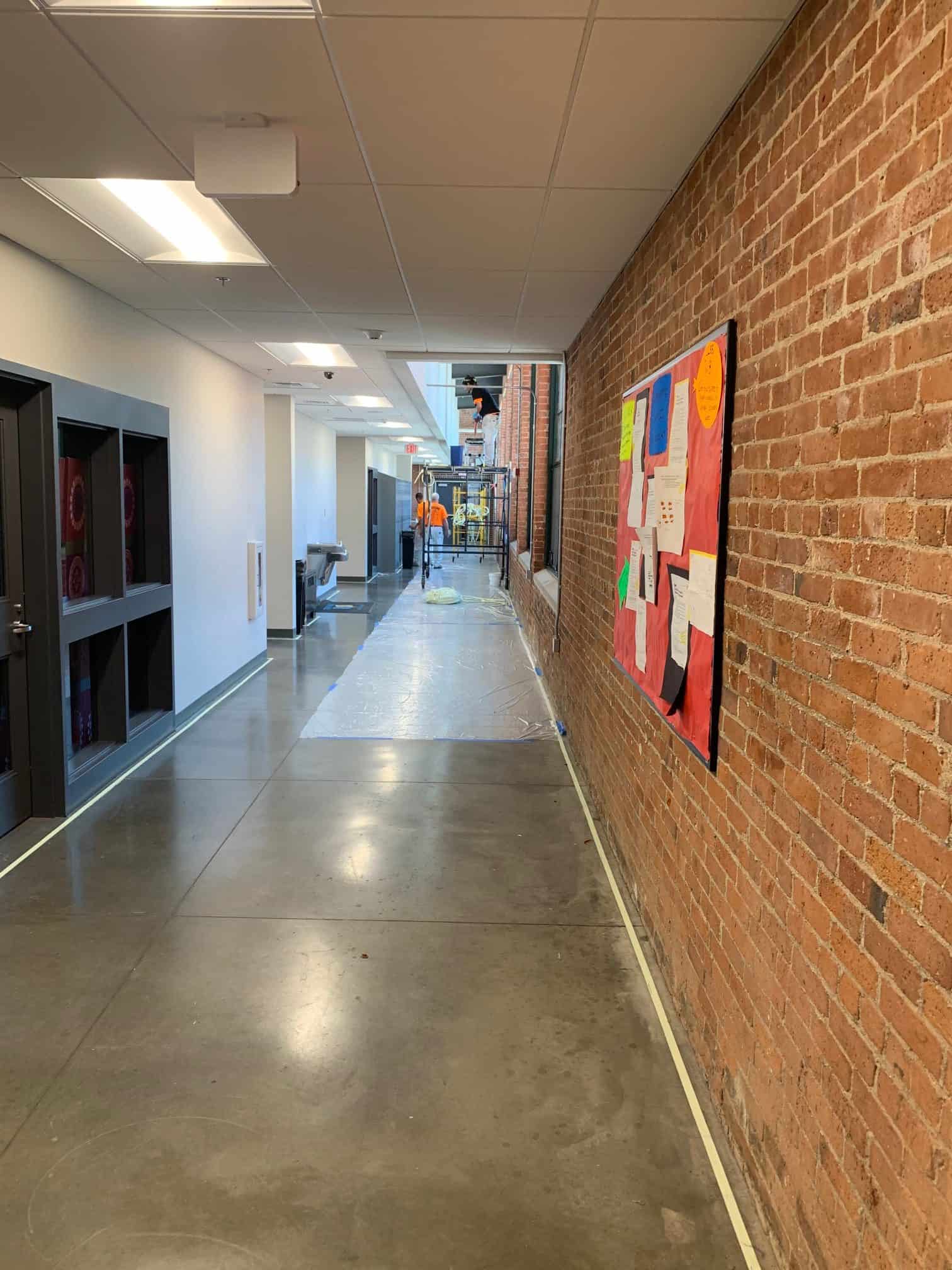
And just like many other towns like it, Bridgeport is bouncing back. It entered a period of revitalization around the start of the 21st century of its downtown and other neighborhoods in need of investment.
For this undertaking, the restoration was two-fold: Part 1 was converting the Howard Avenue building (which formerly housed the American Graphophone Company) into a facility for the town’s Great Oaks Charter School. The three-story building includes 70,000 square feet of space for classrooms and a cafeteria, while 23,000 square feet are devoted to residential apartments for the school’s tutors.
Adjacent to this building on nearby Cherry Street is the second part of the development – Cherry Street Lofts, 157 units of workforce housing in a space previously occupied by a foundry.
In conformance with historical restoration guidelines and in keeping with the owners’ desire, the interior walls of floor-to-ceiling red brick were to be retained and featured as part of the new interior aesthetic of both buildings.
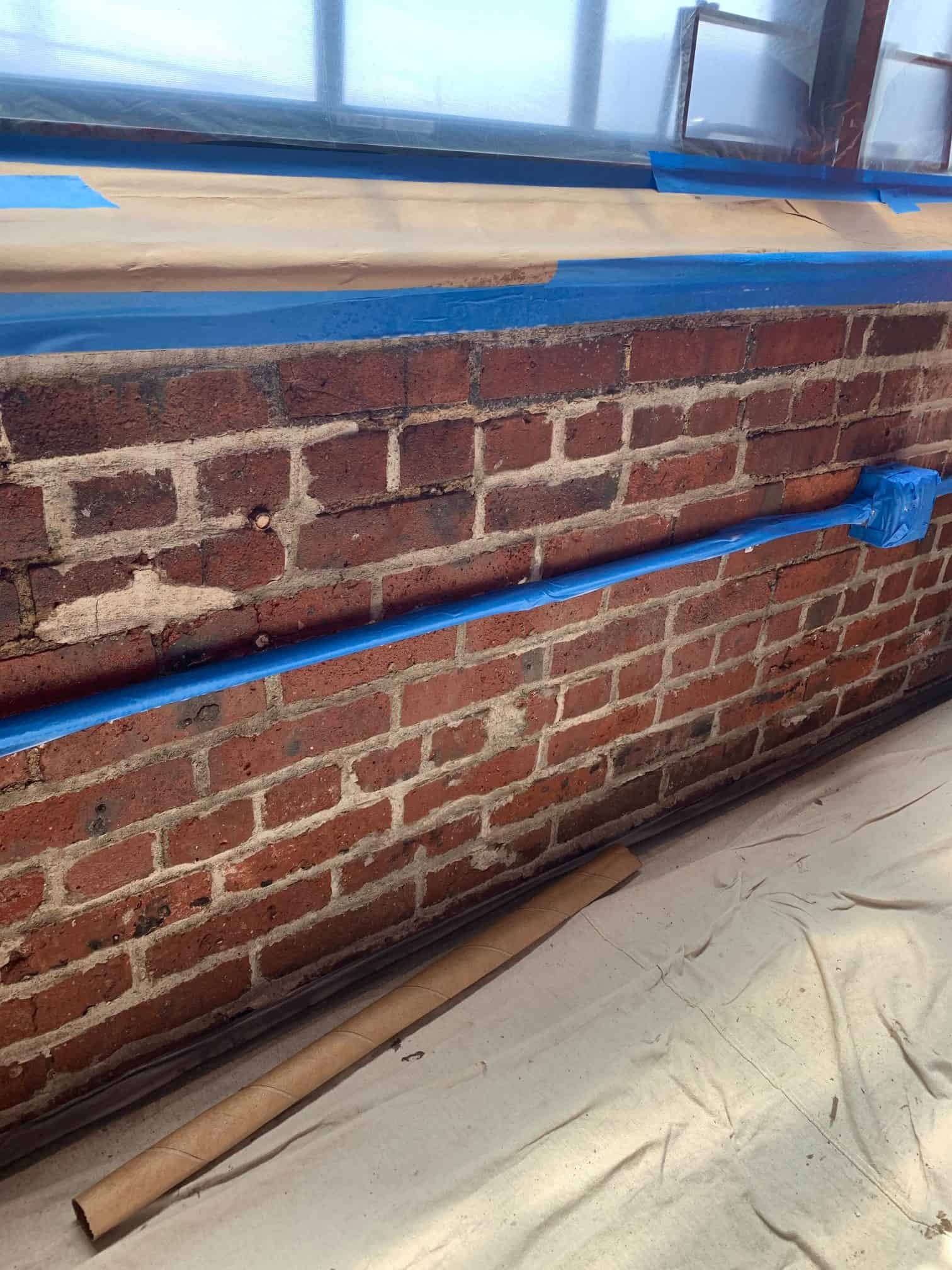
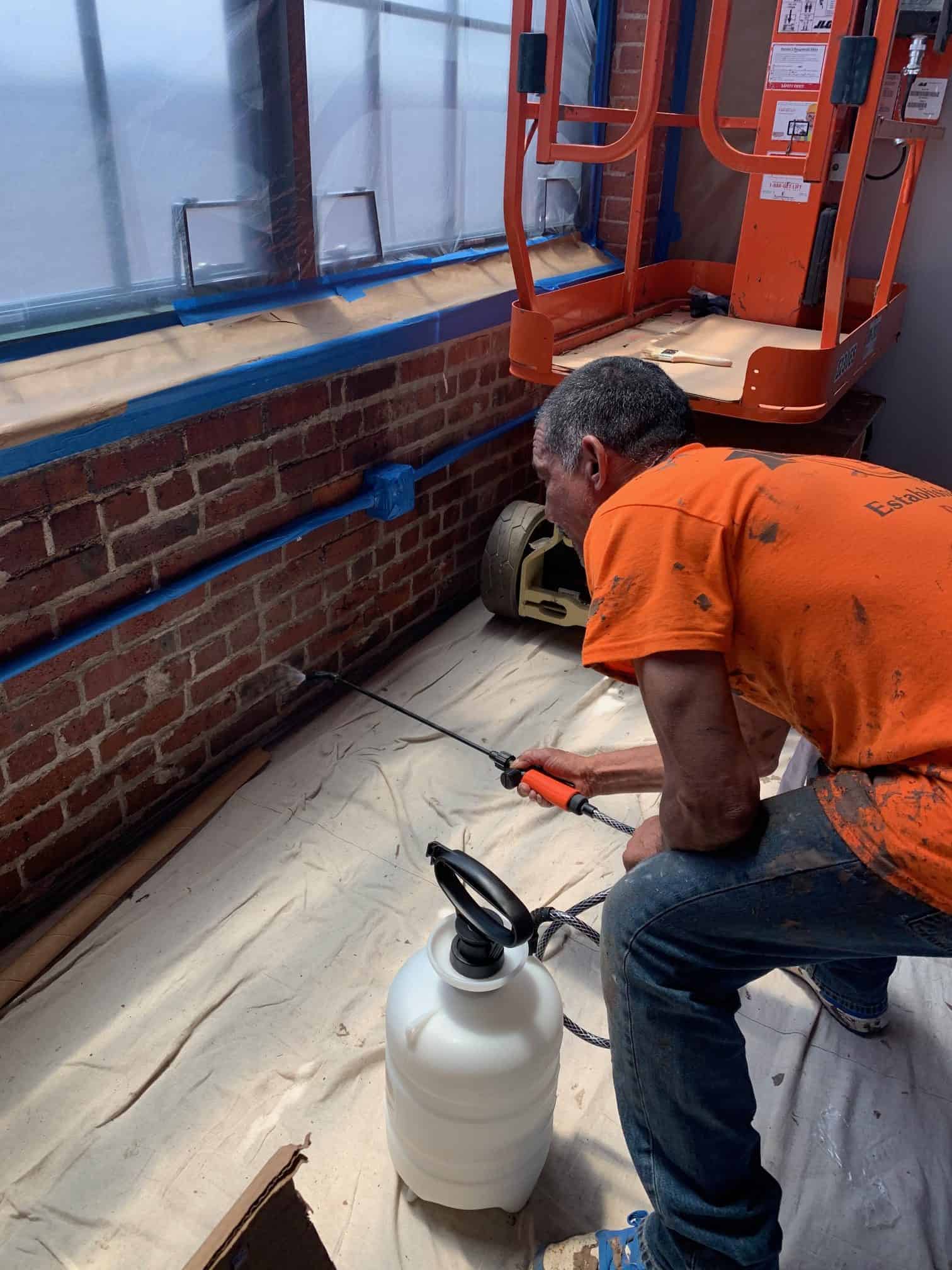
But when the centuries-old brick interiors started creating dust, Flocco knew he needed a quick solution to dustproof the tenants’ living spaces and students’ school environment.
However, a condition of this historical retrofit was to maintain an authentic finish on the brick, not an overly polished one.
“We wanted to keep the brick looking natural and organic, and not leaving any shine or sheen,” Flocco said.
Other dustproofing products on the market that are appropriate for interior use wouldn’t meet standards for aesthetics and performance – some leave a glossy film on the substrate, and others create an impermeable layer on the substrate that can easily trap and seal moisture into the walls.
The painting contractor on the case was Ray Jerry, who’s worked on enough historic retrofit projects to have seen plenty of brick like this that’s “been around since the beginning of time.”
“The owner was looking for a warehouse look, so none of the brick is painted, the beams are all exposed,” Jerry said.
He was confident that the issue of the dusty walls was solvable. His crew was working with a new product from PROSOCO called Interior Masonry Dustproofer. Ideal for interior applications, this product not only is certified by SCS Indoor Advantage Gold for indoor air quality, it’s also Living Building Challenge-ready because it does not contain any Red List ingredients.
Considering his crew was using a product they had never applied before and working on the fly, there were lots of opportunities for things to go wrong. But thankfully, Jerry’s applicators found the product extremely easy to use and made the dustproofing process simple.
“It’s very easy to do, it’s user-friendly, and it works,” he said. “It does what it’s supposed to do.”
Jerry won’t be surprised to be using Interior Masonry Dustproofer again on future restoration projects in his region.
“On historic projects, they want an authentic feel, they don’t want it shiny,” he said. “The look (of Interior Masonry Dustproofer) was very natural. It’s the way to go if you’re looking for that.”