A Leader in the Southeast
When you think of cities leading the charge in green building in the US, many immediately think of Portland and Seattle in the Pacific Northwest. Maybe you think of up-and-coming cities in the Northeast and Midwest like Pittsburgh or Boston. But the Georgia Institute of Technology and The Kendeda Fund set out to write a different story, building a Living Building Challenge 3.1 certified building in the deep South.
“I think it’s going to dispel a lot of myths about how the South cannot have high performance buildings,” said Dennis Creech, Kendeda Fund Fund Advisor for Sustainability. “The South is one of the most challenging climates in the World to design for, but we can do it here.”
The Living Building Challenge is considered to be the most rigorous building performance standard in the world. The humidity and heat of southern summers makes it extremely difficult to design and build a building that is net positive energy and water usage, but the newly opened Kendeda Building for Innovative Sustainable Design on the campus of Georgia Tech hopes to prove it’s possible.
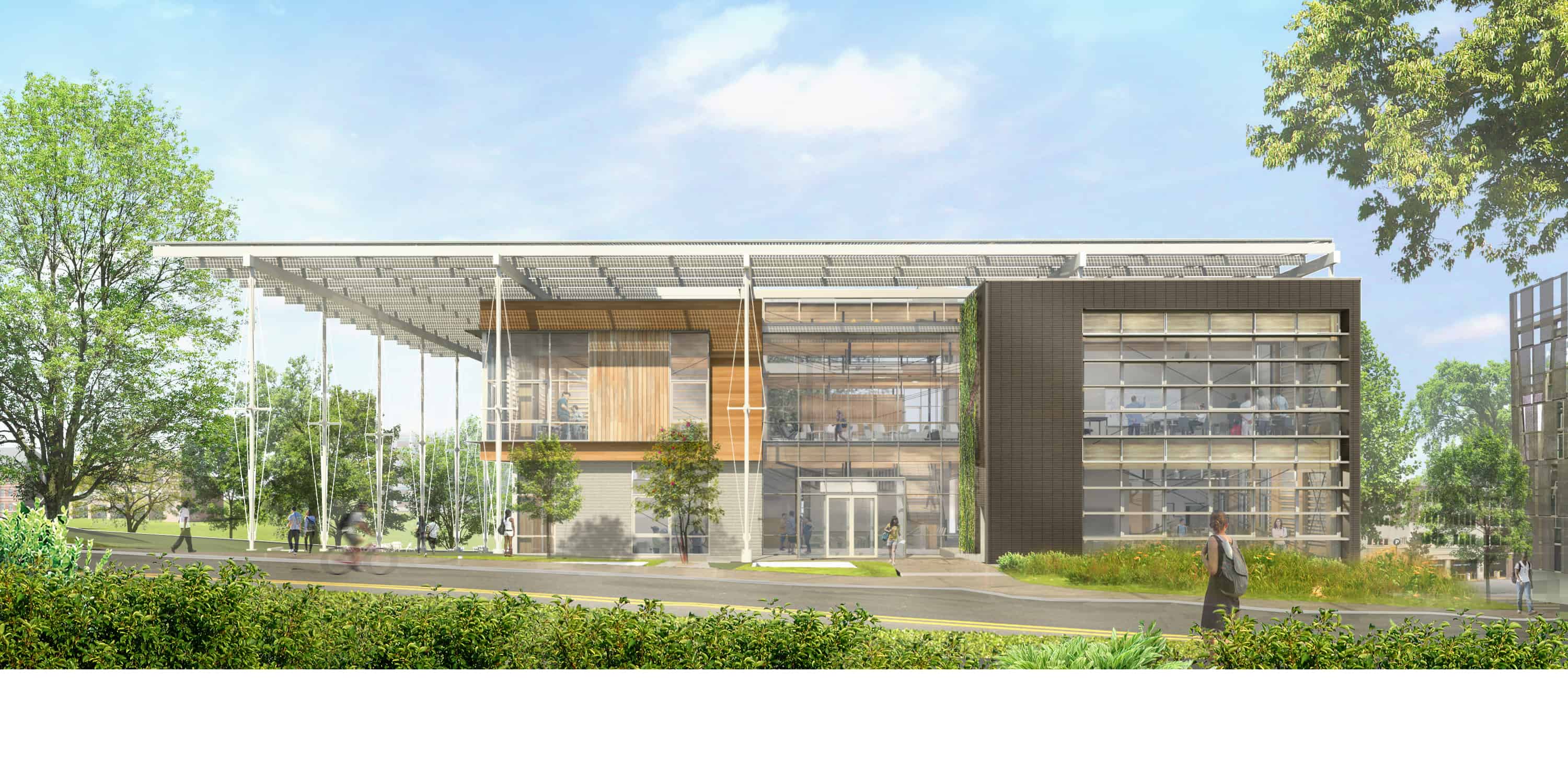
Putting a Plan Together
The design-build team (which included staff and faculty from Georgia Tech as well as project partner leads Lord Aeck Sargent, The Miller Hull Partnership and Skanska USA) put together a plan for a 47,000 square-foot building with a massive porch, beautiful green space and a distinctive overhanging solar roof. They carefully selected all of the materials, avoiding any worst-in-class chemicals on the Living Future Institute’s Red List and designed the water capture and energy systems to meet the net positive targets.
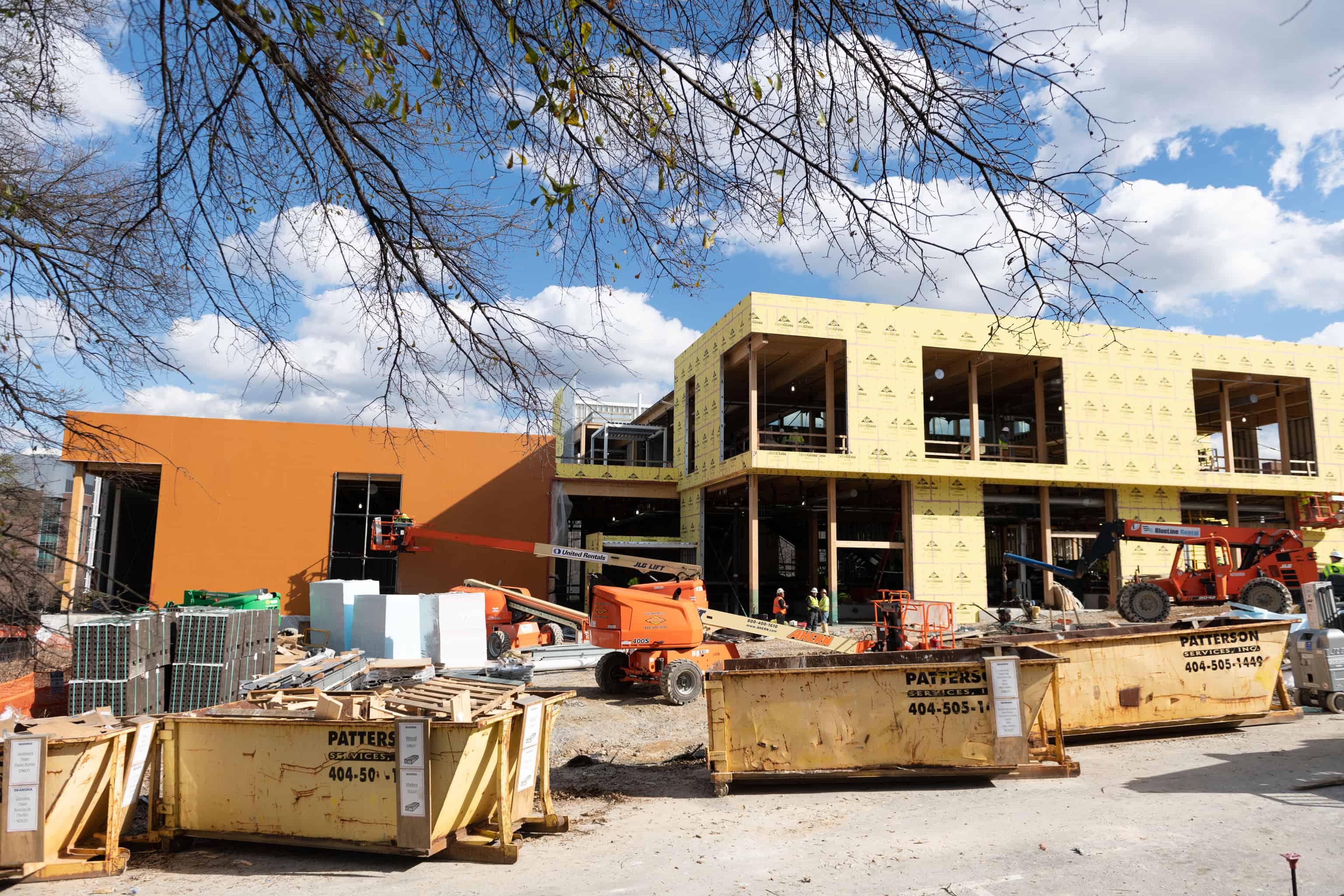
Sealed and Delivering
With high outdoor summer temperatures, it’s critical to ensure the building is sealed up tight from air intrusion. But the high humidity means it’s also just as important that the building breathes, allowing water vapor to escape the wall assembly. The PROSOCO R-Guard air and water barrier system including FastFlash, Joint & Seam Filler and Cat 5 was selected to provide this functionality.
The R-Guard Cat 5 liquid flashing and sealant system got its start in the damp climate of the Pacific Northwest. PROSOCO modified the formulation to eliminate phthalate plasticizers in response to a request by the Bullitt Center design team. This success in Living Building Challenge Red List optimization led the company to change the entire product offering. Since then, PROSOCO has eliminated over 2-million pounds of phthalates, with successful installations in every climate zone in America.
The Cat 5 system is moisture-cured, meaning it can be applied even to damp surfaces or during even the most humid days. With a tight deadline to open The Kendeda Building by the fall of 2019 and the application of the air and water barrier occurring in the spring, the construction team could not afford delays. The fluid applied system was applied easily by roller and could be applied before or even shortly after southern afternoon rain showers.
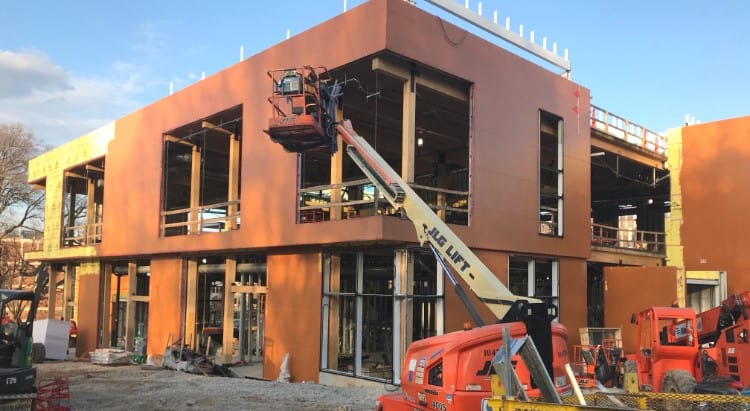
Testing the Seal
Once the envelope was completed and the doors and windows closed and sealed, it was time to test how tight everything was. Even the smallest leak could result in the building missing energy efficiency targets. The team turned to the SK Collaborative to perform a Blower Door test. A blower door test pressurizes the building and measures the amount of air leakage from rough openings or through the wall assembly. A great result on the blower door test means the building is likely to meet its energy efficiency goals post-occupancy.
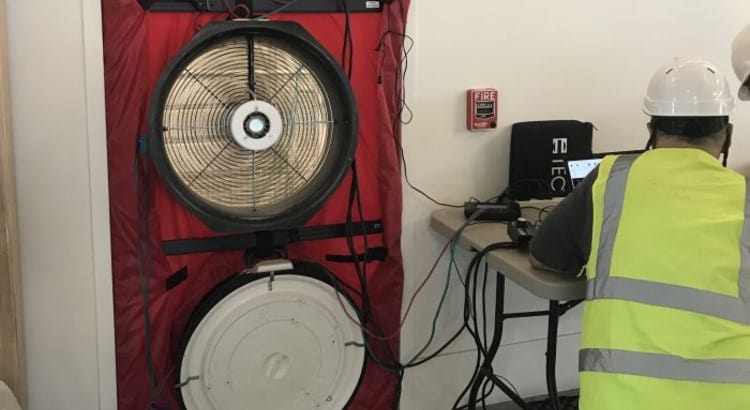
Unfortunately, the first test didn’t quite meet expectations. The good news is that the test was done early enough in the construction of the building that the team was able to troubleshoot solutions. The team identified just a few missing gaskets on the rainwater cisterns and the tightening of a few covers. The wall assembly and the air and water barrier were performing to expectations.
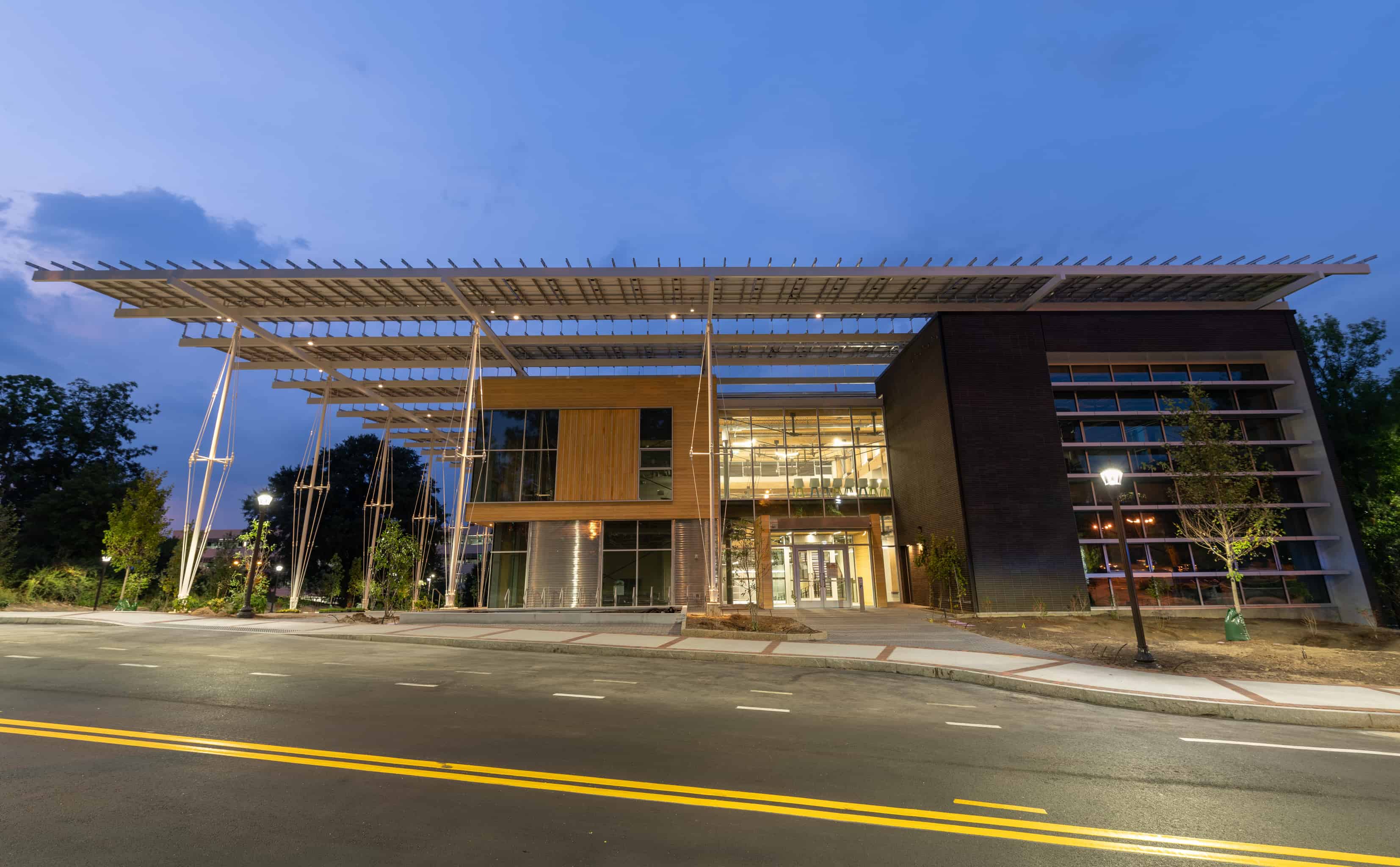
The Challenge is Just Beginning
Now that the Kendeda Building for Innovative and Sustainable Design is open to students and the public, the most difficult phase of achieving Living Building certification has begun. Unlike other green building standards, the Living Building Challenge requires 12 months of proven performance before a certification is achieved. This means modeling for net positive energy and water isn’t enough – you must walk the walk too. Several Living Buildings have taken more than 12 months to achieve this, often troubleshooting along the way. Sometimes a particularly warm summer or dry stretch of weather may cause the clock to reset.
All of us at PROSOCO congratulate all involved with the design and construction of this beautiful, high performance building and wish them the best as they work toward Living Building Certification.
To read more details about The Kendeda Building for Innovative Sustainable Design, visit livingbuilding.gatech.edu and livingbuilding.kendedafund.org.
For more on the Living Building Challenge and the International Living Future Institute, visit living-future.org.