It would have taken half of the turmoil in 2020 for builders, homeowners and health professionals to question the safety levels of indoor air quality (IAQ). Given the COVID-19 pandemic and widespread wildfires, news headlines are rampant with content on the new normal regarding safe air quality levels capable of keeping pandemics and toxic fumes at bay.
As if a pandemic isn’t enough, according to the National Interagency Fire Center’s (NIFC) National Interagency Coordination Center (NICC) by September 27, 2020, 44,447 wildfires will have burned 7,376,721 acres, a whopping 1.3 million more acres than the 10-year average. In California alone, its worst fire year in history, there have been approximately 8,000 fire incidents with more than 3,600,000 acres total acres burned. Oregon and Washington are also experiencing devastating wildfires as well. Into this backdrop of air quality given pandemic and wildfire smoke and soot, there are many things builders and homeowners can do to mitigate the crippling effects.
Good Filtration and a Tight Envelope are Critical
To date, the majority of housing in the U.S. is “leaky,” in that there is no control over the penetration of outside air that leaks in through cracks around windows and doors. The building industry in recent years has taken a more scientific approach, however, making great strides in controlling both water and air intrusion in residential homes. The resulting “airtight” building envelope is highly efficient and highly insulated.
North Americans spend approximately 90% of their time indoors. With all homes, it’s important to exchange the stagnant air indoors with fresh outdoor air in order to reduce the amount of carbon dioxide (CO2) indoors. Advances in building science indicate that when a perfect amount of fresh-filtered, conditioned outside air is introduced, a dramatic reduction of CO2 occurs, capable of doubling brain functionality and reducing respiratory illnesses by more than 75% and also preventing the build-up of mold.
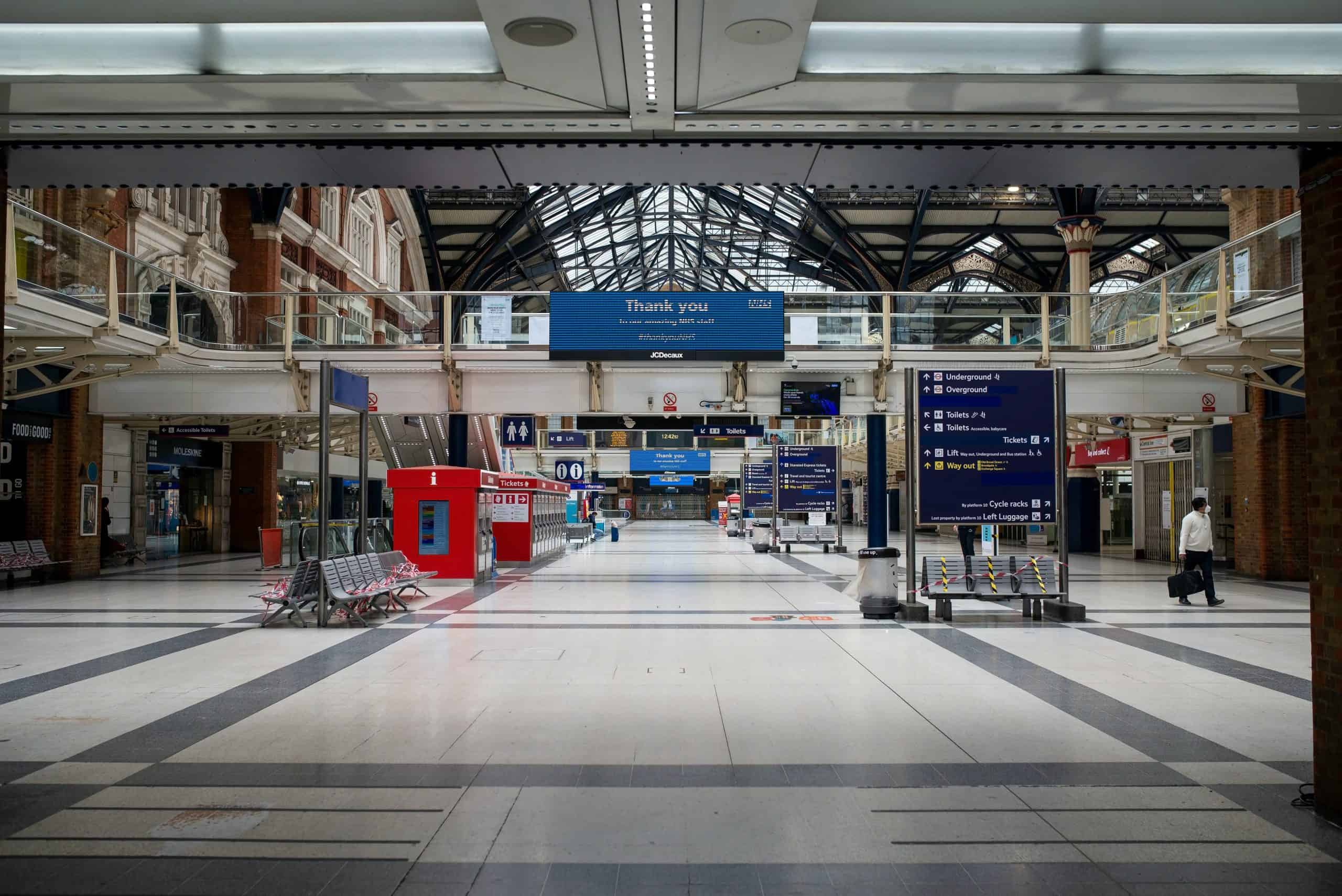
Controlling the air flow is done through a combination of air-sealing and HVAC design. Air-sealing creates a continuous thermal and pressure boundary that tightens the building envelope and maintains control of indoor temperatures throughout the year. It is important to include advanced HVAC designs early in the build process, whenever possible, although it is still possible to achieve the balance between a tight envelope and the introduction of fresh air by retrofitting an existing structure.
Recommended HVAC equipment includes an energy recovery ventilator (ER) for summer months and a heat recovery ventilator (HRV) for winter. These units temper incoming air and also control humidity. In addition, the application of liquid air sealants can be an important step in making sure that there are no gaps to compromise the system. Once sealed, a blower door test should be insisted upon by a homeowner to identify any hidden gaps or cracks where air can still leak through. The building envelope should meet blower door test requirements of less than 1ACH50 (air changes per hour at 50 pascals of pressure differential).
Whether in new construction or homes already built, there are now products that can be successfully used to seal the envelope. PROSOCO and its R-Guard line of air and water barriers, for example, is an ideal system to achieve and maintain control in the conditioned environment.
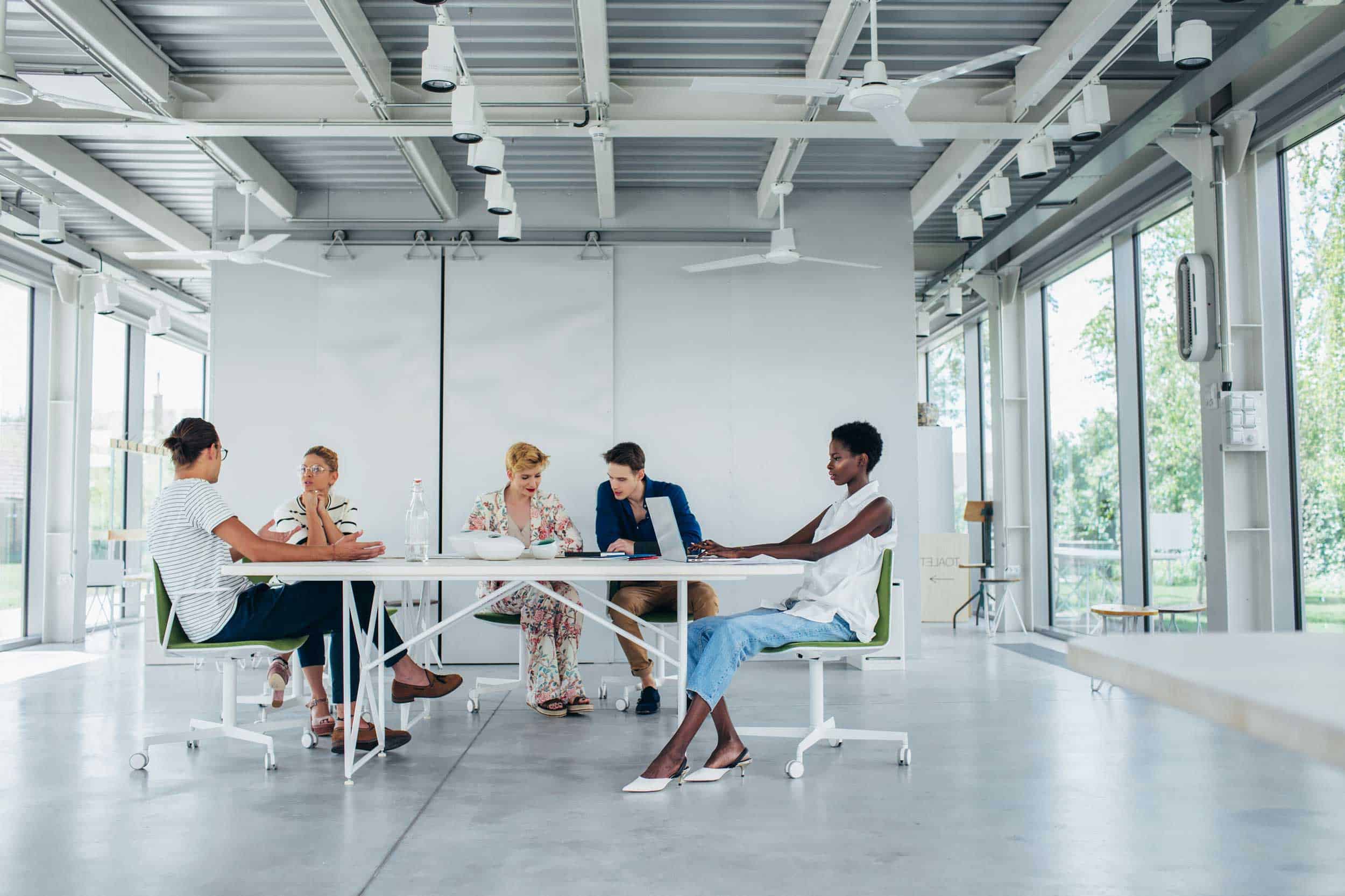
Creating the All-Important Air Barrier
The PROSOCO R-Guard Cat 5 system creates a primary air barrier designed for use over above-grade structural surfaces when combined with the company’s Joint & Seam Filler, FastFlash, and AirDam products. These products create a highly durable, weatherproofing membrane on exterior sheathing, backup walls, and precast concrete. It prevents water and air penetration of the building envelope in wind conditions up to 155-mph experienced during a Category 5 hurricane.
- Joint & Seam Filler fills openings, creating transitions where flexible reinforcement is needed to bridge large gaps and provide continuous support for fluid-applied flashing membranes, waterproofing or air barrier components.
- A liquid FastFlash membrane is used to counter-flash waterproofing and air barrier components in new or existing wall assemblies, and to seal around penetrations and rough openings.
- Cat 5 coats the field of the wall.
- AirDam creates a weather- and air-tight seal around windows and doors, preventing moist, outside air from entering while conditioning indoor air from escaping window and door assemblies.
PROSOCO helps builders and homeowners meet the increasingly stringent standards that are rapidly evolving.
Air Quality Standards
Behind much of the industry’s move to improve air quality is the muscle provided by evolving standards that enabled building envelopes to achieve the tightness we’ve discussed. For example, the 2009 International Energy Conservation Code (IECC), specifies a whole house airtightness limit, and requires homes to have air leakage of 7 or less air changes per hour at 50 Pascals pressure (ACH 50). In 2012, IECC required homes to meet a limit of 3 ACH 50 or less in most climates (CZ3 and higher), and the Passive House program sets the limit at 0.6 ACH 50.
The American Society of Heating and Air-Conditioning Engineers (ASHRAE) 62.2 Standard in 2019 goes further, contributing to the U.S. Department of Energy’s long-term goal to save $2.2 trillion in energy-related costs through a 50% reduction in building energy consumption.
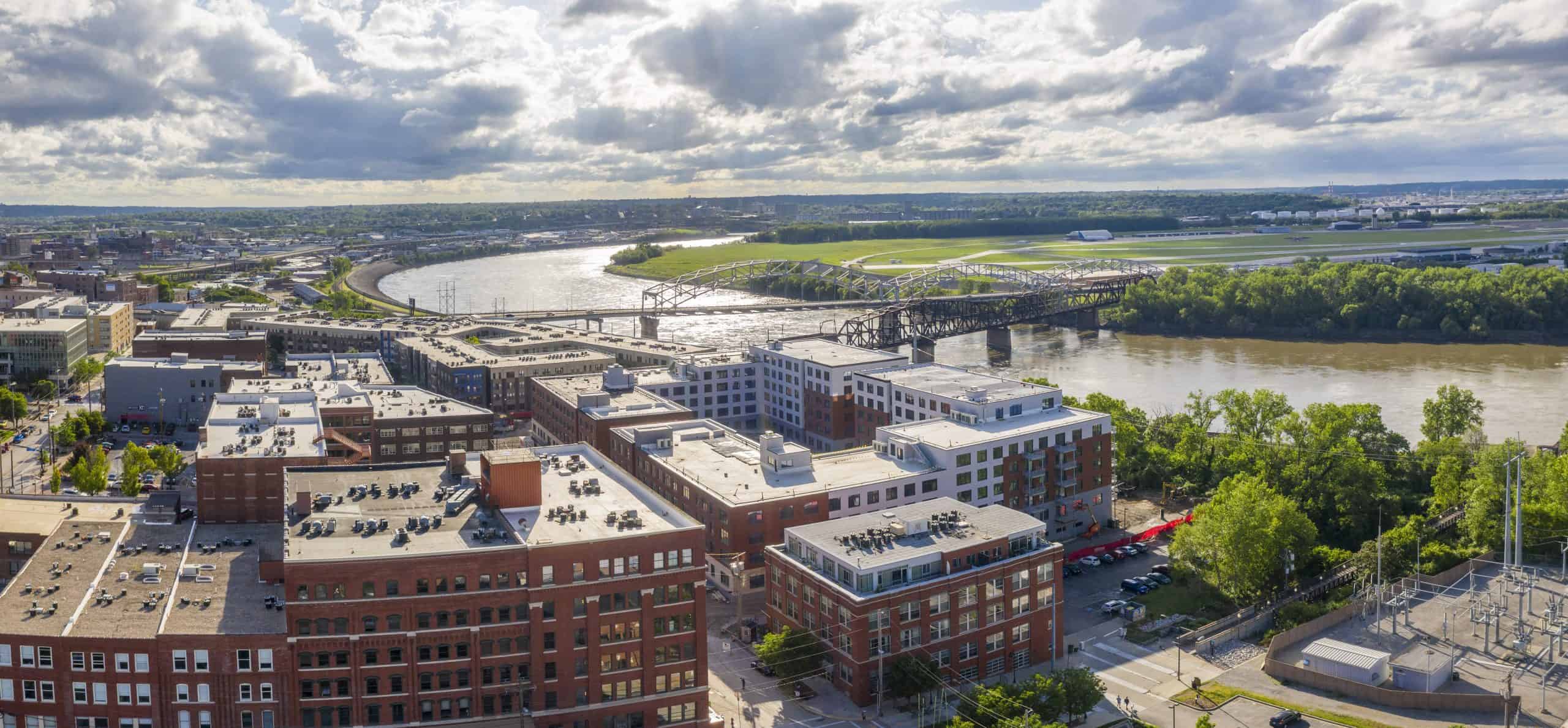
Healthy House Example
For an example of how tight homes and air filtration comes together to ensure occupant health and comfort, Second + Delaware is a 276-unit multifamily project that just opened, becoming the largest Passive House in the world. Located in Kansas City, Missouri, the building features triple-glazed certified windows, and fresh air flow based on a dedicated outside air system (DOAS) that draws fresh outside air into living spaces. The ventilation system and variable refrigerant flow (VRF) heat pumps ensure ideal indoor air quality in each unit.
The project’s 16-inch-thick walls with 10 inches of concrete sandwiched around a 6-inch layer of insulation provides optimal thermal comfort and privacy.
Pandemics, Wildfires and Air Quality
Hopefully, pandemics and the current level of wildfires will subside. What will remain, however, is the need to reduce airborne contaminants, including viruses, smoke, and soot inside our homes. By itself, HVAC systems are not enough to protect us. However, advanced HVAC systems, used in conjunction with filtration and the elimination of “leaky” structures will provide a significantly healthier environment than we’ve been able to achieve thus far.