R-Guard products correct water damage on 6-year-old condos.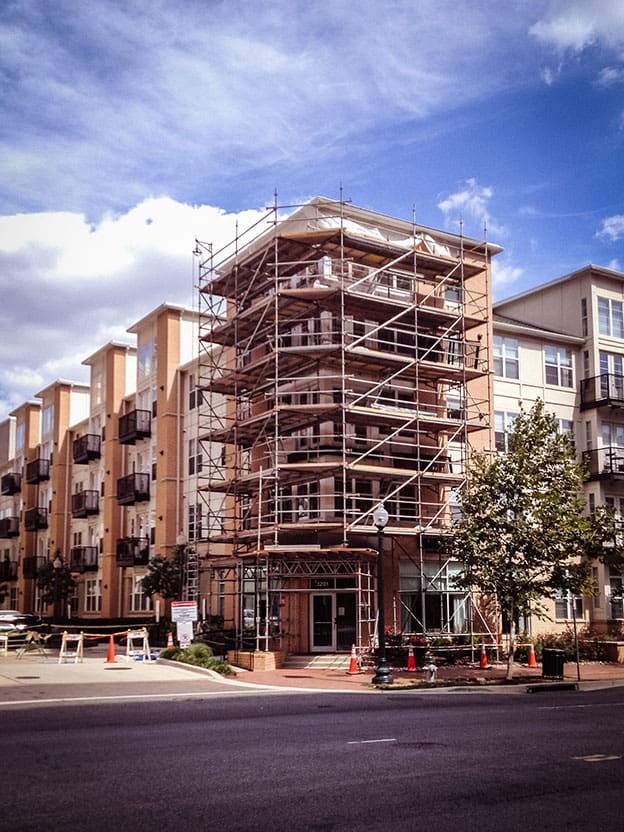
What laid behind the walls of the four-story, wood-framed Silverton Condominiums in Silver Spring, Md., was the stuff of nightmares for building owners and contractors across the U.S.
It started off as a simple sealant replacement job but quickly turned more serious when the unassuming façade revealed potentially catastrophic structural damage.
A project team came together in a remarkable collaboration to complete the repairs on the only 6-year-old building, and did it so adeptly that it was awarded the Sealant Waterproofing and Restoration Institute’s Trinity Project Award with its “Sealants Save Lives” entry. The project team – Facility Engineering Associates, Standard Restoration & Waterproofing Co., and PROSOCO, met the award’s criteria of demonstrating exceptional partnering efforts between teams comprised of an SWRI contractor, manufacturer and associate member.
“Usually that level of damage is seen on structures 10 to 15 years old. To see it on a building that age was pretty dramatic.”
Behind a pretty face
Built in 2007, the residential Silverton Condominiums began showing signs of leaking issues in the winter of 2013. The building owner brought Facility Engineering Associates (FEA) on site to assess leaks on the structure’s east/west corner that frequently takes on significant amounts of wind-driven rain. Over six years, this recurring weather event coupled with the condos’ French balcony doors, part of the building’s original design, eventually resulted in visible leaking to tenants.
“With leaks the only outward sign something was wrong, the client believed the caulking simply needed to be replaced,” said Steven Bentz, the engineering consultant on the project with FEA. “But after an initial visual inspection we recognized suspect conditions with cladding and general construction and recommended that a contractor be brought in to open up the skin of the building and determine what was really going on underneath the façade.”
With the thumbs up from property management to dig deeper into the building’s issues, FEA tapped Maryland-based contractor Standard Restoration and Waterproofing (SRW) to tackle the project alongside them. With FEA’s worst-case scenario scope of work in hand, SRW arrived on site, erected a pipe frame scaffold and installed interior, insulated partitions to reduce weather exposure and create a suitable investigation and demolition/work zone.
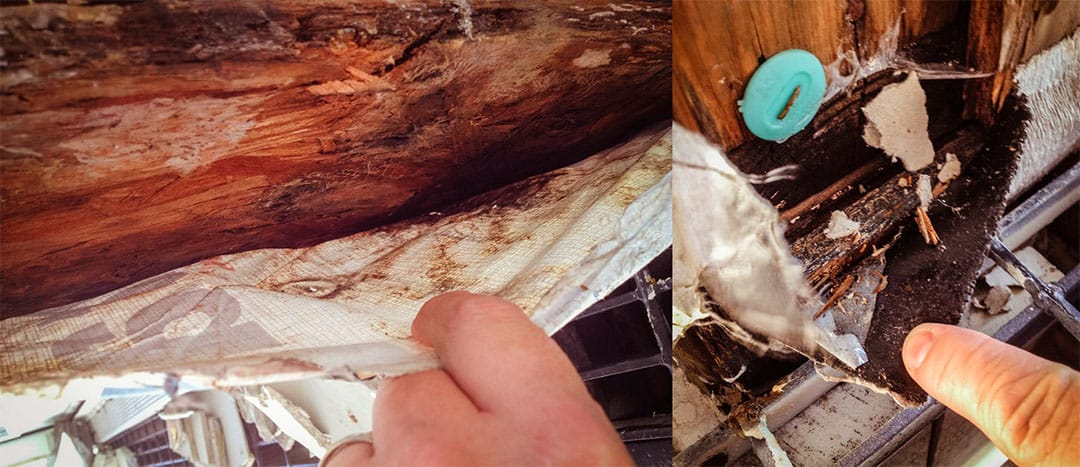
The perfect storm
Demian Weaver, Mid-Atlantic sales manager for waterproofing systems manufacturer PROSOCO, the third player of the Silverton team, echoed Etchison’s concerns. “We see this situation all the time. It occurs often from non-permeable products being applied to damp surfaces, and then the degradation starts right away. Throw in the element of regional environmental factors and you’ve got damage happening in buildings even younger than Silverton. In fact, we’ve seen structural damage on three-year-old construction.”
“There were large, multiple structural wood framing members that had been essentially reduced to cardboard. Unfortunately we see this type of deterioration frequently.”
Where the waterproofing began its downward spiral specifically at Silverton was with the application of a cladding system that did not allow water to sufficiently drain or evaporate. Water that drove through the non-permeable system by way of open gaps in the exterior cement panels then found its way to a faulty water-resistive barrier. With nowhere to go, the water saturated the wood structural components with every weather cycle for what ended up being six years too long.
After a complete assessment of the deterioration, including measurements and up-close reviews of components, the project team determined that the damage spanned from the bottom of the second floor to the underside of the fourth, with isolated locations around the window assemblies.
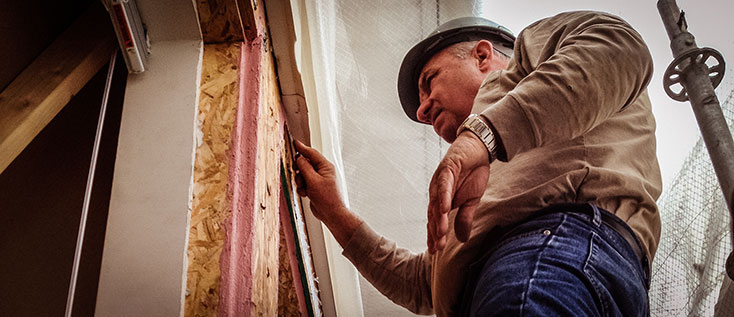
The right way
Given the extent of damage, yet despite additional costs and extended timelines, the entire project team at Silverton—FEA, SRW, PROSOCO, and the client—agreed that a structural restoration was the best and only way to proceed considering the health and safety of the public and the building’s tenants. A new project plan was then created to protect all parties involved, including the public, from the unpredictable conditions in the walls.
“The good news for the client was that in the process of getting an initial price from SRW, we carried an allowance based on our previous experience with jobs such as this,” Bentz said. “Luckily for the owner, the revised scope and price was covered by that allowance and no change orders were needed.”
The expanded scope of work now included shoring and temporary support needed to remove and replace deteriorated wood framing with newly designed structural members and connectors, removal and re-installation of existing windows, replacement of the building’s French doors with sliding glass ones, and finally a complete building envelope approach to the application of a new and vastly improved air and water barrier system to prevent any more leaks at the buildings east/west corridor condo units.
High expectations were set for the new sealant system and involved meeting all detailing requirements to encapsulate the corner assembly and the capability of being applied quickly to potentially wet substrates, as well as during and despite of any variety of weather events.
Aside from material quantities, a piece of the puzzle that did not have to be found and added to the project’s scope was the intended new waterproofing system. From the job’s onset, PROSOCO was named as the manufacturing component of the Silverton team, with the intention of using the company’s R-Guard Cat 5 air and water barrier and sealant membrane system to do the job right.
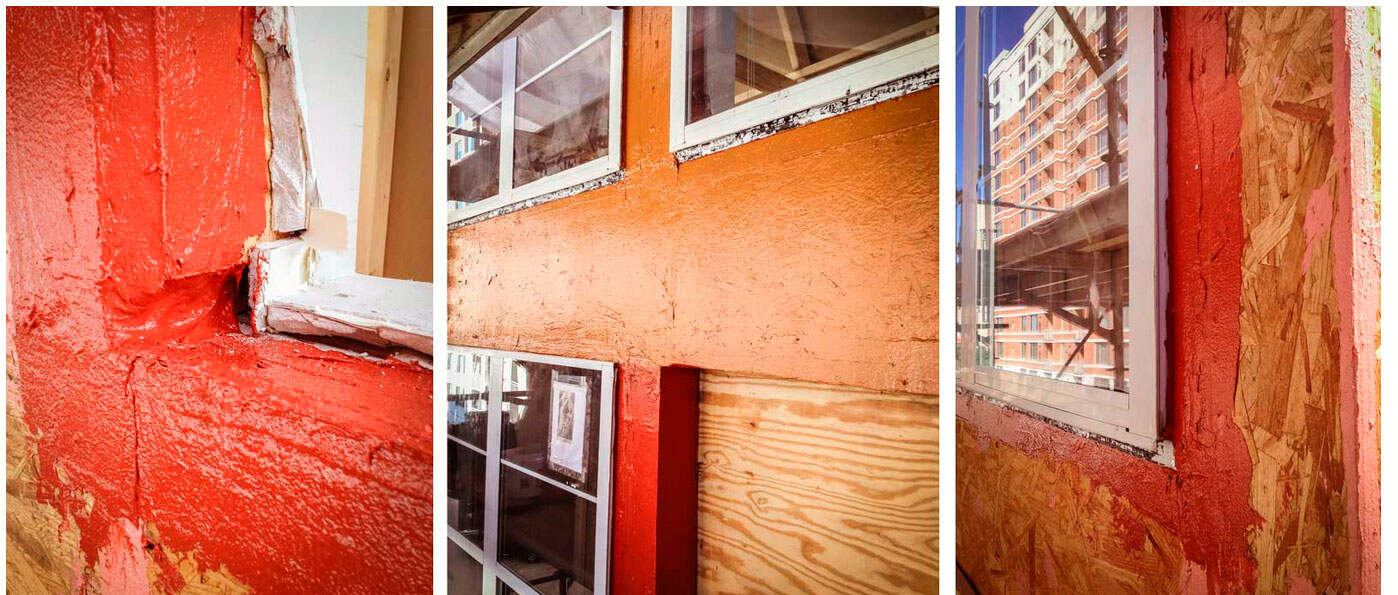
“We had previously done a job with SRW working with the R-Guard product line and wanted those products in the scope at Silverton from the get-go because the system can go over wet or damp substrates,” said Bentz. “During the renovation we did encounter some pretty serious weather conditions, in which the R-Guard products’ weather and temperature stability were critical. This system was the way to go for all the ‘what if’s,’ and we certainly encountered a lot of those on this project.”
PROSOCO, based out of Lawrence, Kan., has been providing construction restoration projects with materials for over 75 years. The company’s products have been part of retrofit and restoration work on the U.S. Capitol, Grand Central Station, and the World Trade Plaza, to name a few. “We’ve used a lot of PROSOCO’s other products over the years,” Etchison said. “The fact that they sell and endorse this waterproofing system speaks volumes, because they really do their homework.”
All elements of PROSOCO’s R-Guard, Cat 5 waterproofing system—Joint & Seam Filler, FastFlash liquid flashing membrane and AirDam air and weather barrier sealant for windows and doors—feature unique silyl-terminated polymer (STP) chemistry that makes them immediately waterproof upon application, and enables the products to be applied to damp surfaces. So rather than using an exterior sealant approach that depends heavily on the waterproof integrity of individual cladding components and assemblies, the Cat 5 system is easily roller-applied, producing a seamless, durable elastomeric weatherproofing membrane for a variety of façades —free of seams, open corners, and/or layers.
The final step in restoration at Silverton was the application of the Cat 5 system by SRW’s crew. With the durable, elastomeric assembly completed, the building’s new wood components were now protected from any water that may be retained within the exterior cladding components going forward.
“Waterproofing materials are evolving and we’ve been excited to use the Cat 5 system,” said Etchison. “It’s an extremely user-friendly product that provides a huge advantage to the installer who now doesn’t have to be concerned with applying materials to a damp surface. Using products with STP technology simply eliminates a lot of commonly made errors. Plus, the fact these products do not have weather restrictions for application is a big deal in terms of a project timeline.”
While the east/west corridor of the Silverton Condominium project was the focus of this job, PROSOCO outlined how its FastFlash product, an adhesive and detailing compound that also features the STP chemistry, could be used as a liquid flashing membrane to fill exterior wall openings and terminate the membrane of adjacent wall components on the other façades of the building.
Late adaptors beware
With products on the market such as the R-Guard Cat 5 system that are clearly safer and, safe to say, better options than their waterproofing predecessors, the question becomes why are projects like Silverton so commonplace—especially on relatively young construction? According to Weaver, “Waterproofing products with STP chemistry like the R-Guard line have been in the market for a little over a decade—so not very long when you’re talking about the construction industry. These products are not widely accepted yet, but we’re steadily educating people, working to change the mentality, and opening minds to the idea, especially in our market.”
Weaver added that while price is always an issue, in terms of these products, it matters more in the residential sector than the commercial. “When you’re building 2,000 homes there’s a significant change to the bottom line to incorporate these products versus the standard stuff, but on the commercial side, the price point is right in the ball game.”
Etchison, who’s been a contractor for 30 years, said while habits die hard in the construction industry, he sees the industry heading in the right direction. “It’s my experience that they have to learn a hard lesson first before making a change, and seeing how the investment at the beginning is worth it in the long-run—or not so long—in the case at Silverton. Those lessons are coming sooner than intended for some and so I see a gradual shift in the value placed on better products by the industry.”
A hard lesson aside, what was avoided at Silverton was a very serious collapse of structural members that could have resulted in tragedy not perhaps that day, or the next, but likely in a year or two, said Bentz. “The damage was that severe and had progressed to the point where there was deflection and movement in the building. By the time FEA got on site, pressed to its full design load, the building would have just been capable of holding its capacity—just. In another year, with the same weather patterns, it likely would have lost a member or two to collapse,” he said.
The project team at Silverton completed the job in February of 2014 and to date there have been no additional leaks reported.
As for the team’s recognition from SWRI, Weaver said it’s all about the team. “The Trinity Award win wasn’t so much about the project or the products, but about how this team accepted the unforeseen challenges of a job and really came together to get the job done the right way.”