When we introduced the PROSOCO R-Guard FastFlash air and waterproof barrier system, we knew a big market would be in coastal areas subject to tropical storms and hurricanes.
That’s because FastFlash is tested and proven to stop air and water leaks through building envelopes in conditions up to and exceeding Category 5 hurricanes. We even call the primary air and waterproof barrier component of the system “Cat 5.”
I’ve put out some feelers to see if there’s any information about how FastFlash products performed in the face of Super Storm Sandy and the following Nor’easter. I know Rutgers University is one place FastFlash is on duty.
For now though, I think we’re all more interested in seeing the effects of our prayers and Red Cross donations in that stricken area.
But along with storm-prone coastal areas, an interesting secondary market has emerged for the FastFlash system.
Ultra-energy efficiency
We’re seeing FastFlash increasingly selected for Passive Houses and other super-green, ultra-energy-efficient buildings. One recent Passive House project is the Karuna House in the Willamette Valley, Ore. A long-time enthusiastic advocate of green building is having the Karuna (means “compassionate” in Sanskrit) House constructed as a showcase for green-building.
The contractor, Hammer and Hand in Portland and Seattle, sealed the plywood sheathing and rough openings with the FastFlash system. They like it because it’s so easy to use.
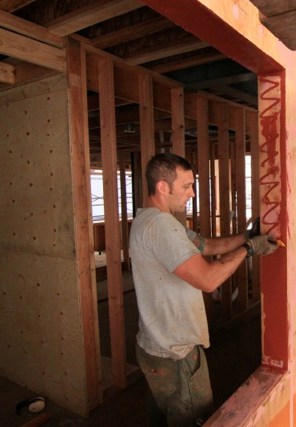
The FastFlash system has also gone on the under-construction Bullitt Center in Seattle. The Bullitt Center is being constructed to an environmental standard beyond LEED Platinum. When certified, it will be a “Living Building,” having met the requirements of the Living Building Challenge — arguably the most stringent environmental standard on the planet.
We didn’t plan for or market to the ultra-energy-efficiency market, but getting specified for it is no surprise, either.
Paul Grahovac, our air barrier product group manager explained why the FastFlash system is a good fit for Passive Houses in a presentation to the 7th Annual North American Passive House Conference, in September.
Sam Hagerman of Hammer and Hand, and Florian Speier of Zola Windows, Boulder, Colo., joined Paul in the presentation. Zola Windows makes windows for Passive Houses, among their other offerings.
Their presentation showed how Passive Houses eliminate air leaks around windows — a common source of higher heating and cooling bills and wasted energy in traditional construction. Passive Houses, which operate on as little as 10 percent of a typical home’s energy costs, can ill-afford any energy-wasting air leaks.
Watch: How to install FastFlash with Natalie Daleney

Measuring airtightness
Air changes per hour (ACH), a measurement of airtightness you get from blower door testing, are a big factor. That’s how you measure air leakage, or lack of, in Passive Houses. Other buildings, too. We tested two window-installation mock-ups in our Design Verification Test Chamber. One mock-up used sheet wrap with peel and stick membrane. The other was our fluid-applied FastFlash system.
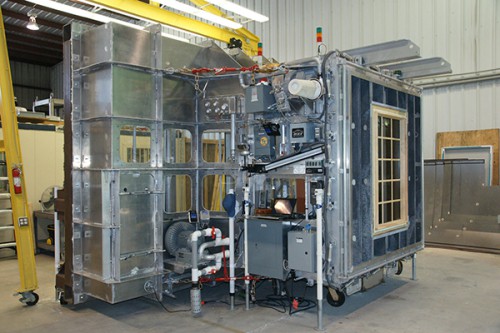
We cranked the air pressure to 50 Pascals, simulating a 20 mph wind. This test was similar to ASTM E2357, which reports the volume of air loss per square foot of mock-up wall. Since this test was done specifically for the Passive House conference, we did the math to convert the ASTM-type results to blower-door results in ACH50 (Air Changes Per Hour, 50 Pascals).
Perspective and results
Here’s a little perspective. To get an Energy Star rating, your blower door test must be within 6 ACH50 in Climate Zones One and Two, 5 ACH50 in Climate Zones Three and Four, 4 ACH50 in Climate Zones Five, Six and Seven, and 3 ACH50 in Climate Zone Eight. To be certified as a U.S. Passive House, the house must test below 0.6 ACH50.
Here’s the ASHRAE Climate Map, not that it matters — the sheet wrap and peel-and-stick membrane mock-up did not quite make any of the Energy Star levels. It tested at 7.01 ACH50.
The FastFlash mock-up tested at 0.17 ACH50. That’s quite a bit below the airtightness standard required for Passive House.
We found this level of performance to be true in the field as well.
Hammer and Hand conducted a preliminary blower-door test on the Karuna House with some minor areas of the FastFlash system yet to be installed. They achieved 0.42 ACH50.
For fun, we cranked the air pressure in the chamber to Category 5 hurricane level. That’s 2,880 Pascals, equal to a 155 mph wind. Even under those conditions, the FastFlash fluid-applied mock-up delivered 0.53 ACH50.
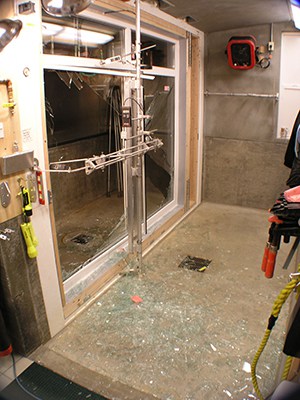
One time we raised the pressure so high in one of the chambers that we blew out the glass before we could get the FastFlash to leak air. But that’s another story.
Paul also cited some of the reasons designers and builders are moving away from fabric wraps and peel-and-stick membranes for detailing rough openings — backed up by Sam Hagerman from Hammer and Hand:
•Rotting of damp substrates behind vapor-impermeable barrier coverings
•Reverse lapping
•Tenting
•Tunneling
•Fishmouths
•Heat damage
•Adhesion failures
•Difficult, laborious work and human error
•UV damage
Every one of those items is a definite no-no for a Passive House, or any other building that strives for energy efficiency.
Paul, Sam and Florian finish off their case for FastFlash and Passive Houses with this info:
Installer experience
Physical actions required are pulling the handle on a caulk gun to lay down a bead of material, and spreading it with a piece of flat plastic. Even inexperienced workers are successful in their first attempts. Application speed and material conservation increase with experience.
I keep harping on how easy the system is. The fact is, I’ve installed it myself during a window replacement at my own house, and NO ONE is less of a DIYer than me.
Material availability and durability
FastFlash products are available at hundreds of construction supply distributors across the country.
The service temperature of a leading peel-and-stick membrane is 158 degrees F with a maximum UV exposure of 30 days.
FastFlash products have been tested to 300 degrees F and may be exposed for up to six months. They do not rip or tear, and any gashes into them can quickly be repaired by re-coating.
Material and labor cost
Labor costs vary based on location and experience, but ease of application cuts installation time, thereby cutting labor cost. The FastFlash system can be applied to damp surfaces, unlike most if not all other air barrier products. This eliminates many weather-related construction delays. And the instantly waterproof system doesn’t have to be protected from rain while curing.
PROSOCO had to add a second shift during the recession to keep up with demand fueled in large part by contractors switching jobs to this system to lower their costs of doing business.
These are all reasons why the Passive House and ultra-energy-efficiency market is embracing FastFlash — and why other markets are too.