Our answers to 6 questions from building envelope consultants and design professionals
Members of PROSOCO’s Building Envelope Group recently presented a webinar for Building Enclosure titled, “Retrofitting for Energy Savings and Health Concerns in Today’s Climate.” You can watch the full webinar on-demand through November 2022.
Several architects, consultants, designers and spec writers in attendance of the live event submitted some really insightful questions, which, unfortunately, we were unable to answer due to the time limit. We were able to connect individually post-event to answer the questions, but we realized that if a handful of design professionals asked these questions, there were likely many others who would find the answers useful. Here is our QA to those questions in condensed format, with the following panelists:
Question #1: We have a project that will have the siding removed to do repairs and to better air-seal the building. Currently, the building has a ½-inch foam board sheathing. Are we better leaving off the foam board and adding a half-inch of OSB over it and then air-sealing? Or should we remove the foam board and just add the ½-inch OSB and then air-seal?
Paul Grahovac: First of all, I’ll assume that “foam board sheathing” is meant to indicate a foam applied to the studs without any kind of rigid sheathing. My personal view is that I would take it off and put OSB over it, then air-seal it and then come over the top with some kind of insulation.
Guy Long: I think the question is relative to the perception that the foam is going to add some degree of insulation. But I tend to agree with Paul Grahovac’s analysis from the standpoint that it's always better to apply the OSB board, deal with the seams first, and then come back and apply an air barrier over the top of that. Then the thought process about providing an insulation layer can be dealt with appropriately.
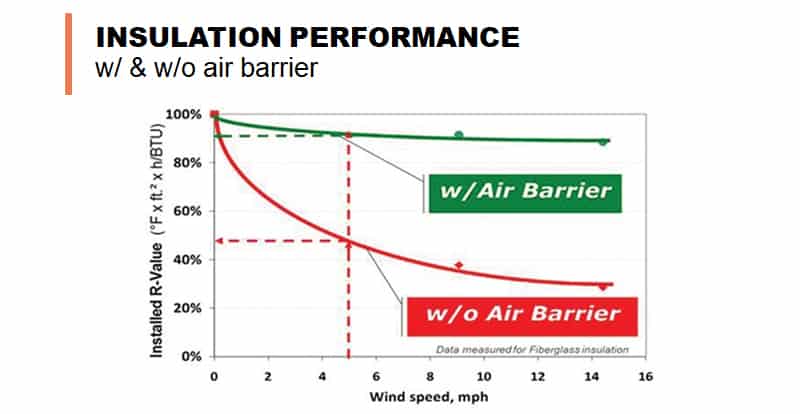
QUESTION #2: I saw an illustration showing that insulation performance is poor when there is not an adequate air barrier, and that it’s good when there is an adequate air barrier. Does that apply to batt insulation only, or to other insulation types? (Slide pictured above.)
Paul Grahovac: I know the illustration or graph they’re talking about, and that correlation is true because the test for insulation performance and R-value is a laboratory test that assumes a high degree of air tightness. And so what the questioner is saying is that OK, presumably, does that apply to batt insulation? But what about other insulation types? And here I think they could be talking, for example, about continuous external insulation. And so what I would say is first, I think I want I would like to credit Ryan Dalgleish with the Air Barrier Association. I believe he developed this information and graphic. But continuing here, my view would be that this graph is focused on batt insulation, and the reason is that if you have continuous external insulation, you're getting a significant contribution to air-tightness because of the continuity of that material. Now, of course, you know there are issues about whether the seams between the pieces of rigid insulation are sealed or not. But I would say that a separate analysis would probably need to be undertaken for exterior insulation. This is a classic case of the batt insulation, in my opinion.
Guy Long: Paul, I tend to agree with what you're indicating, it is always in the best interest of the person that is doing some retrofitting that an air barrier will always provide the means in which the performance of the insulation would increase dramatically, whether it was batt insulation or some other type. I feel very strongly about the fact that with an air barrier, you're going to find the performance characteristics, plus the fact that it's a layer of protection that you're dealing with, that will automatically start to take place for the performance of the insulation.
QUESTION 3: Could you please elaborate on how we can introduce fresh air to the building interior with low impact cost?
Paul Grahovac: I'll just give a little background on this without going the wrong way around the pond. Basically, PROSOCO published a paper in the journal of the International Institute of Building Envelope Consultants (IIBEC) which basically collects a lot of existing information about how increasing the outdoor air component of the HVAC circulation can dramatically reduce the risk of coronavirus transmission. And so the questioner’s asking, “Well, how can you do that with low impact cost?” The first thing I want to clarify that I believe the questioner knows and others may as well, but I didn't know until I started looking into it -- that increasing the outdoor air component of the HVAC circulation is simply a matter of a quick and easy adjustment on a damp or a vent that your facilities manager can readily achieve. And I'm not trying to be flippant, but that's how you do it. So really, the underlying question, I think, is, well, if you are increasing the outdoor air component, you're going to have more unconditioned air to condition, then that's going to cost more. And so I will address that question. First of all, PROSOCO has been running approximately 25% outdoor air since the first earliest days of the pandemic. And they haven't had a problem with cost or with humidity, which is all often raised as an objection to doing this. They started running at 30%. They found that the comfort level at 72 degrees was not acceptable. They dropped it to 25%, which is still very high. And I found that was the sweet spot. Again, the first question is, maybe there is not a significant cost. Then to further the question on cost - what can you do? Well, some people would refer to it as a graded approach. You could go for a complete energy retrofit and dramatically reduce your energy consumption, both through airtightness, insulation and say, perhaps, high-performance windows that would be at the far end of the cost spectrum. And I'm eager to hear what the other guys would say, but my understanding is that simply interior sealing the window-to-window-frame interface has been shown to have a dramatic impact, and I think there's also potential for doing some interior sealing with respect to other parts of the building.
Guy Long: Well, that's the key. If you can render the interior space much more airtight, then the control and the cost associated with that control is reduced dramatically. We do get involved with doing an analysis of that, and it's not that we're the HVAC people, but we work hand-in-hand with the HVAC mechanical engineering group to look at the airtightness of that particular structure. And once we determine that or apply a means in which to prevent the passage of unconditioned air getting in or being able to dehumidify, and the conditioned air from getting out, that's what saves the money.
QUESTION 4: Could you please talk a little about how to introduce an air barrier in the negative side of the exterior building wall?
(combined with…)
QUESTION 5: What is the most economical method to seal an air barrier with a brick masonry facade, multi-family building that has no waterproofing or air barrier?
Paul Grahovac: You know, I'm going to combine question #4 with question #5, because they’re related. I want to mention that sometimes what you don't hear addressed in these circumstances is what to do with the exterior face of the masonry wall. You're going to hear from my colleagues what you do on the interior. But since typically in these types of air barrier retrofits, you're also introducing interior insulation, that means that the exterior face of the masonry will no longer be heated by the building during the winter. And if it is taking on water, it's going to exacerbate the tendency toward freeze-thaw damage. So what should be contemplated in addition to evaluating all your downspouts and repointing missing mortar and such, is the application of a clear penetrating water repellent to help assure that masonry does not take on water and exacerbate the freeze-thaw. So with that, I'll hand it on to you guys about how to do an interior retrofit.
Guy Long: From my perspective, PROSOCO has a way and a means to deal from the negative side. It is our STP (silyl-terminated polymer) formulation in which we apply it to the negative side of the building, such as historical applications or the retrofitting of big masonry facilities being transformed from a big mill building that housed a lot of machinery, to people in a townhouse kind of transition. A situation where we're changing the entire dynamic of that particular building. Repurposing is a good word. The point is that we can deal with it, but you have to look at the whole building and work very closely with the HVAC mechanical engineer to understand the dynamic because you are changing where the dew points are going to take place. You're going to have to be dealing with reinforcement steel that perhaps is already in the brick at this point. You've got to do everything and look at all of the aspects of that particular building in order to feel comfortable that you're not going to be causing more problems than you are trying to help. So again, that's something that we do have available. We do provide it more specifically for retrofitting or repurposing projects, especially with older and historical buildings.
One of the things that you can do from the PROSOCO side of the equation is not only do we have the water repellent side of the equation, but we have the consolidation and the strengthening of the facade that we've been doing for the past 80 years. And there's not many other companies that have that level of expertise to be able to analyze it and to make recommendations on cleaning as well as preserving the very, very fragile masonry surface over long periods of time.
Paul Grahovac: I’m glad you bring up the strengthening and the cleaning, which is also part of it, but people are not as familiar with clear penetrating water repellents and their efficacy as they should be.
QUESTION #6: The Centers for Disease Control recommendation of 100% outside air and the HVAC distribution conflicts with HVAC operation and energy efficiency goals. Any thoughts on how to achieve a balance?
Paul Grahovac: I quoted some numbers in the article I mentioned previously on COVID and ventilation. These aren’t my numbers. I'm not an expert in this and neither is PROSOCO. I recommend everybody makes their own evaluation and ask their own experts. But this is what my research disclosed. Basically, that most schools, for example, are operating at 2.5% outdoor air in the HVAC mix, and that means that the balance of the air is just being recirculated and that's done for energy efficiency. But that was pre-pandemic. Even pre-pandemic, ASHRAE (the American Society of Heating, Refrigerating and Air-Conditioning Engineers) was recommending 18%. But obviously, that was not being done in the schools, and I can gather that the school number is probably pretty much what was being done in offices as well. And just as an aside, if you bump the number up from 2% to 18%, the cognitive function of the occupants increases by 100%. The study talked about in the paper said, what happens if you move from 2.5% to 8% or 10% outdoor air? What impact did that have on coronavirus? Well, with respect to the main means of spreading coronavirus, which is the aerosol that travels far from 5 feet away, hangs in the room and is present when the infected person leaves, and it can infect a person who comes into the building after the infected person is gone. That is the main means of transmission, and if you move to 18%, you eliminate that risk. It is as if you vaccinated 100% in the building, if I remember the article correctly, so that’s worth checking out. So you get a dramatic improvement. It makes you wonder, well, how much higher do I have to bump 18% to get to take out an even bigger percent of those large droplets. And there is no silver bullet on this. But the University of Colorado has an extensive program that they've developed for coronavirus to address these issues. And this has been reported in Time Magazine and National Public Radio. They have an online calculator. If you have someone that's good with spreadsheets, for example, you can play what if scenarios. But when one of the leaders of that program were queried on Twitter and asked, 'Oh, come on now, give me a number.' It was 30%. And so that just happens to match with what PROSOCO found to be the maximum they could operate without comfort problems, you know, 25%. So if I had to recommend a rule-of-thumb number, I'd say 25%.
Follow-up question to #6: Are there any other entities out there that are addressing the feasibility of 100% outside air and what that would mean? What it would cost to condition 100% outside air? And how much more energy that would take?
Paul Grahovac: Well, there's a lot of people talking about it, writing papers about it and such on the specific question of 100%. You know, people in infectious disease like to go there and the HVAC people don't. But there's a way to pull it off, and it's called the DOAS, a dedicated outdoor air-handling system. And what this means is instead of bringing in all this additional air (the concern being humidity and energy costs than anything else) and if you're going to try to run a high level over 25% of outdoor air, you've got to start working with your building envelope. The best way to do that is to build your building to Passive House, and Passive House does not just mean houses. There's a 26-story Passive House dormitory that just got built in the middle of New York City, by Cornell University. There's a 376-unit apartment building, the largest Passive apartment building in the world, which was recently constructed in Kansas City. So this is real stuff and the levels of energy consumption are so incredibly low that you can more than pay for what you're going to increase your energy bill by when you're bringing in this additional air. So, that's the way you handle 100% and you can do retrofits to Passive House as well. And then the only issue is the humidity. Again, if you're going to go above 25% instead of bringing in all the air with the water vapor in it and then trying to get your air conditioner (which is not designed to be a dehumidifier, it just does that as a byproduct of cooling air), you're faced with not being able to remove enough of the water vapor. You put a dehumidification system on the front end of your HVAC so as the air is coming into your building, it goes through this DOAS and that knocks water vapor out or down significantly, and now your HVAC unit has a much easier load to deal with so that it is cooling dry air. So it’s a combination of airtightness and dehumidification. There is a brand new facility in Bethesda, Md., a mixed-use office facility, where they're bragging about how they're running 75% outdoor air for pandemic issues. So we're not making this stuff up. People are going for it.
Guy Long: I think it's very important to bring up the fact that PROSOCO is very active and involved with Passive House. I know, Paul, you're very active. Passive House provides that comfort level within the interior, but at the same time provide all kinds of benefits for the people on the interior that enjoy that, especially from the active pathogens in the home, and people who have allergies. That significantly impacts each one of the people that are in those buildings and from an energy perspective, it very easily can be achieved. I know that the Department of Energy is looking for that 2030 net-zero kind of condition. So Passive House is the path that we have to go down. PROSOCO has been taking the lead from a manufacturer perspective, and I’m very proud of that and to be involved in that perspective.