By Jake Bruton, Aarow Building
When builders consider energy efficiency, one standard is at the top of the list. The Passive House standard establishes such criteria as space heating and cooling demand, renewable primary energy demand, airtightness, and thermal comfort. These are achieved through five Passive House principles: thermal bridge-free design, superior windows, ventilation with heat recovery, quality insulation, and airtight construction.
Given that Passive House helps guarantee comfort, indoor air quality, and operation costs, these things can only be achieved with control over the building envelope.
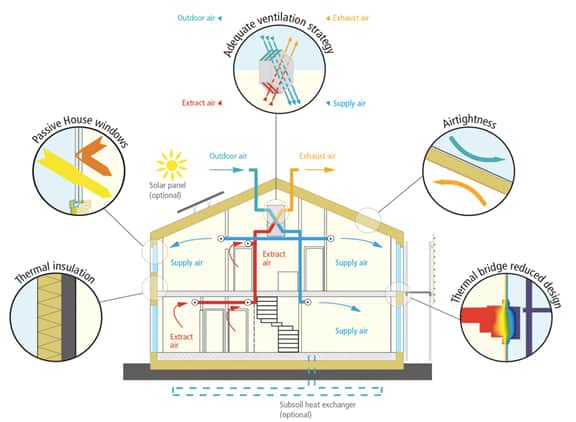
Taking Control
Taking control in a project aiming to meet Passive House certification means appropriately managing the water, air, vapor, and heat that moves through or across our assembly. The easiest of these to manage is heat flow. We know, for example, that adding insulation to our assembly in stud bays or continuously on the exterior of the building appropriately slows the movement of heat. Water, air, and vapor, however, are more challenging.
Controlling water, air, and vapor must be carefully executed. If we have a hole in insulation, it potentially causes comfort issues. Comparatively, a hole in the water control layer will likely result in damage to the structure. This is also true for air and vapor. Air moving through the assembly brings potential moisture in the form of vapor and pollutants we don’t want inside our buildings. Continuity is critical, and one of the simplest ways to achieve a continuous control layer is by using fluid-applied membranes over an entire assembly.
The Benefits of Fluid-Applied Membranes
Buildings have corners, openings, and undulations with potentially uneven surfaces. When it comes to products that connect to all surfaces in an easy-to-execute way, fluid-applied products allow material to contour and flow into all hard-to-reach locations. PROSOCO’s FastFlash and Joint & Seam Filler, for example, connect rough openings, panel joints, and fastener penetrations. This is the first step toward continuity and, therefore, control.
At this point, builders can follow traditional construction methods with a multitude of possible and familiar sheet goods. Once all of the connections and penetrations are connected, a monolithic fluid membrane in the form of Cat 5 can be rolled or sprayed over the surface of the entire wall. This process allows builders to create one continuous watertight, air-tight, and vapor-open assembly with little added effort and minimal experience.
Finally, add PROSOCO’s AirDam to install an air control layer on the interior face of windows and doors for assemblies that can drain at the face of the wall but still maintain plenty of air sealing and drying potential.
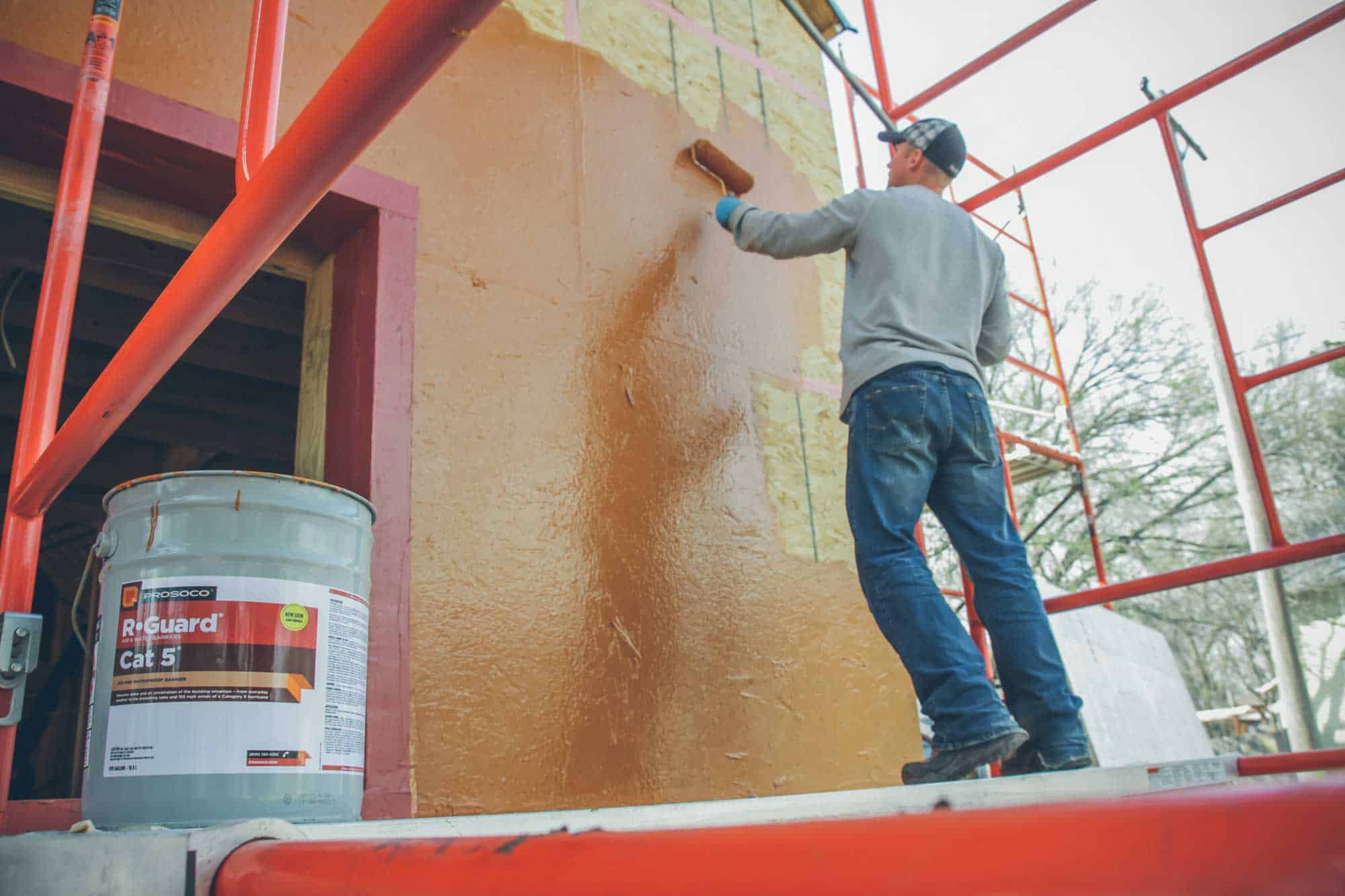
More Control and Flexibility for Less
In the not-so-distant past, fluid-applied membranes required costly equipment and/or specialty contractors. PROSOCO’s products generally require fewer crewmembers to install than competitive sheet goods or large roll membrane products. One person, for example, can apply PROSOCO’s FastFlash, Joint & Seam Filler, and Cat 5 in a solo operation, freeing other crew members for different tasks. In addition, PROSOCO’s products provide the flexibility a contractor needs in scheduling, ease-of-use, and cost.
Ultimately, achieving Passive House control and adequately managing the challenges of water, air, and vapor is much easier when high-quality products are used for all building envelope surfaces. This ensures the control of comfort, indoor air quality, and operation costs of buildings that today's builders rely on and their customers demand.
Watch: How to install FastFlash

How to install Joint & Seam Filler

How to install Cat 5

How to install AirDam
