This Columbia, Mo.-based residential builder prioritizes education and balance.
Landyn Smith, owner of Black and White Construction in Columbia, Mo., knows what air barrier products he prefers for his residential construction business, but not everyone in the central Missouri region has heard of the fluid-applied R-Guard system, especially homeowners.
“A lot of people in my field are old school and they do what their dad knew, and that’s what his grandpa knew and that’s just what they did,” he says. “There’s not a lot of education behind building science in general.”
"I've used the cheaper product, and it is a bear to work with and it costs me more in time and labor. Your product is best in terms of workability, longevity, applicability, everything."
Smith, who says 90% of new residential builds in Columbia are lumber with OSB exteriors, likes to use the R-Guard system of Joint & Seam Filler, FastFlash and Spray Wrap MVP. When those products are being rolled on to one of his projects, he tends to get a lot of questions.
How he explains it depends on who’s asking.
“If it’s the people buying a home, I’ll have a general conversation about a tighter home and energy efficiency,” he says. “For builders and contractors, it goes one of two ways. One is, ‘What is it and what are the benefits?’ And the other way is about why are you doing this.”
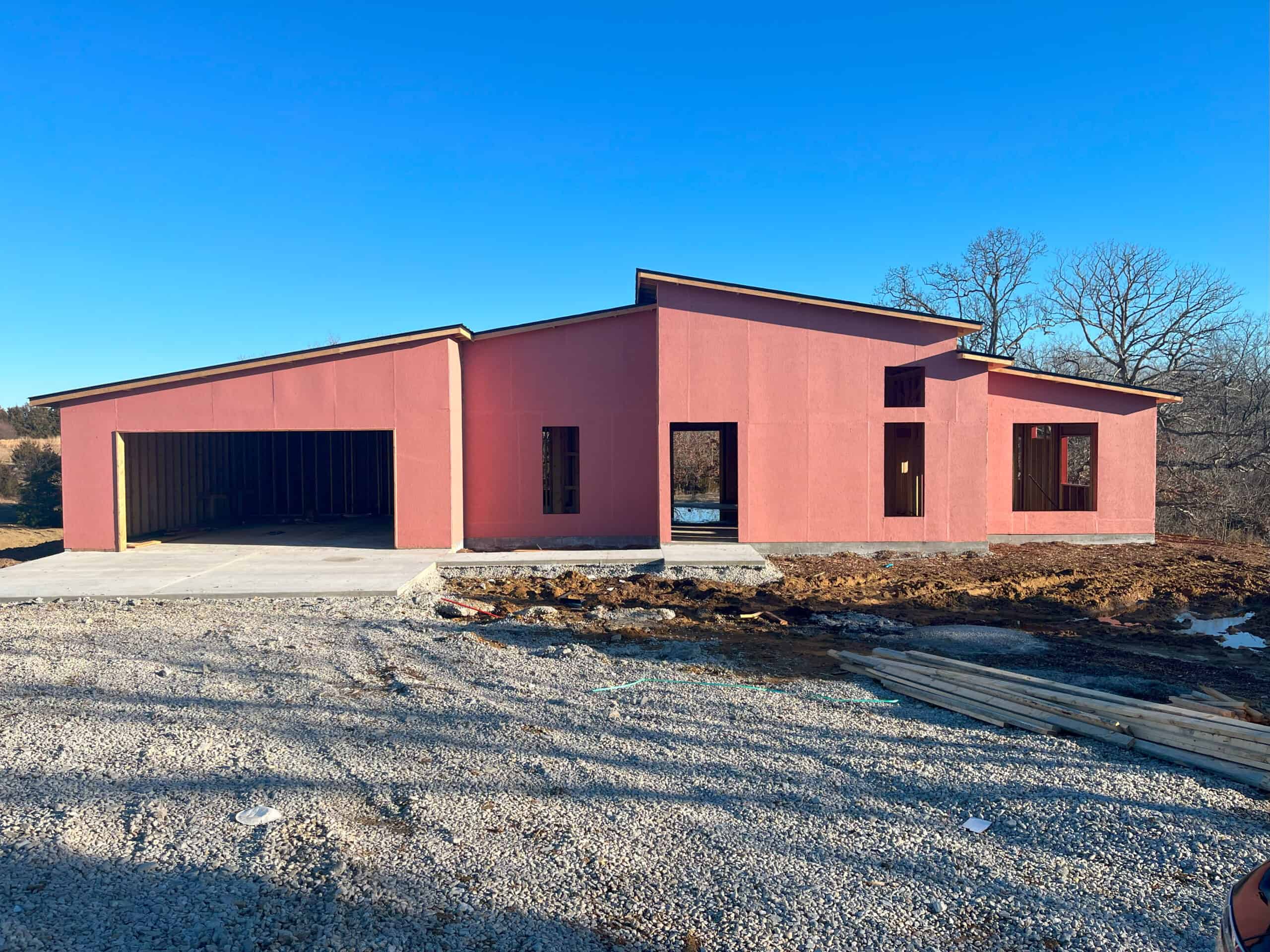
When fielding homeowner questions, Smith says he explains the fluid-applied R-Guard system as an upgrade. “This is an additional service we provide,” Smith says. “The biggest thing is educating. If they do want to dive into it, I’m more than happy. I’ll tell them the three-step process and how each one is applied and then how it prevents problems, and I can go down a rabbit hole. But as soon as I see their eyes glaze over, I think ‘OK, I’ll start wrapping this up.’”
Either way, these conversations are critical to Smith as the contractor as well as the sub or the homeowner. Luckily, his background in sales helps make these conversations easy. What puts some homeowners at ease is hearing what Smith would use on his own house.
“I’d use Cat 5 on my house, which is maybe overkill in my region, and it’s definitely above code,” he says. “But that’s what I’d use on my house. On the other homes I do, I’ll apply two layers of Spray Wrap MVP.”
"I bought my first home when I was 21 or 22. As I started getting into construction, I was upset that I spent so much on it. I realized I could physically do all of this. Then I got fixated on building my own home."
Prior to that, he fills seams and the bottom plate-foundation transition with Joint & Seam Filler, and rolls FastFlash around window openings.
When making a decision between house wrap or a fluid-applied air barrier system, Smith agrees the costs appear different on the surface, but wishes more people took a more holistic look.
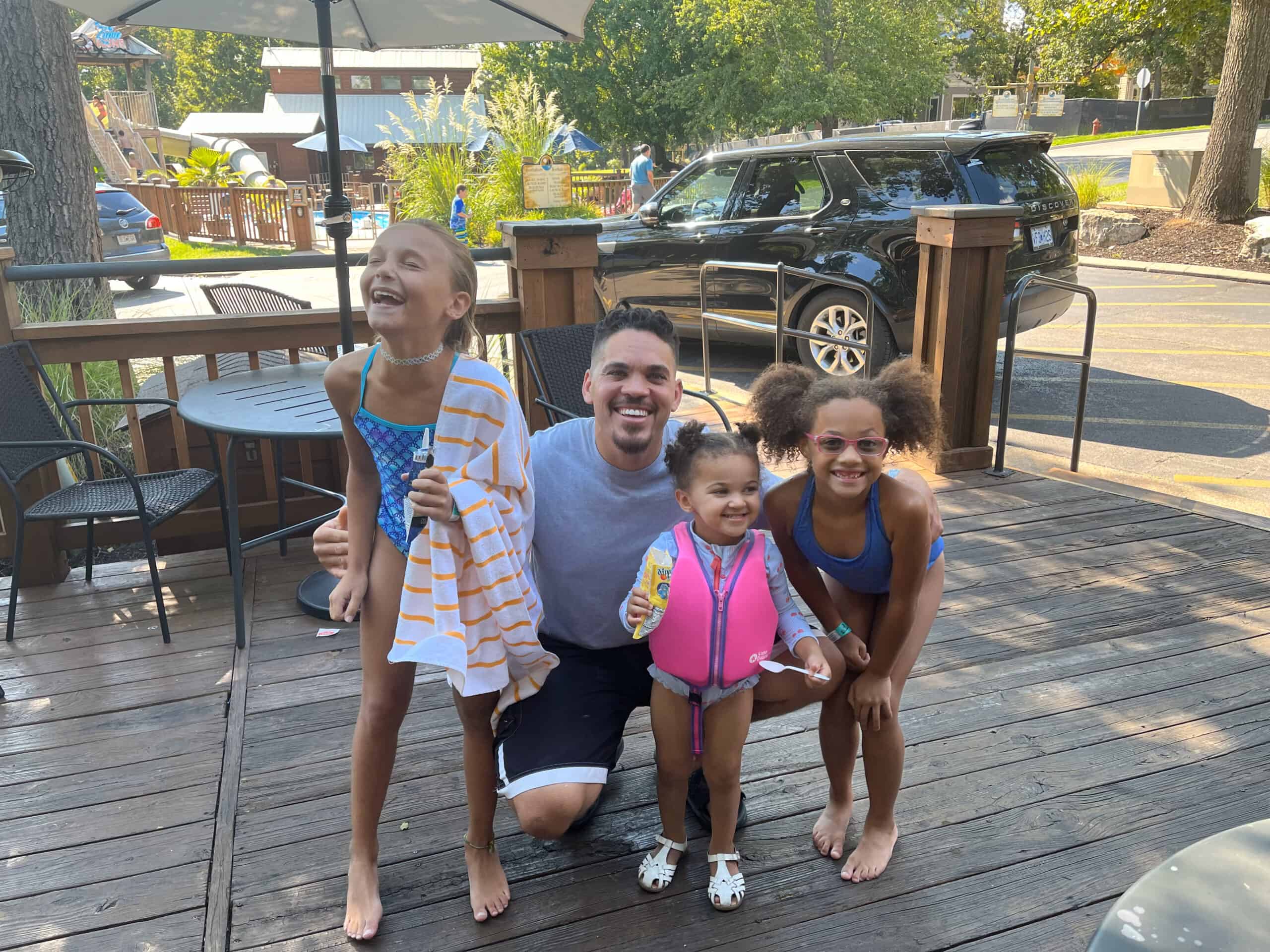
“Your product is the best product in terms of workability, longevity, applicability, everything about it,” he says. “I’ve used the cheaper product, and it is a bear to work with, and it costs me more in time and labor to work with it. With Joint & Seam Filler, I put it in my sausage gun, spread it out and it’s easy. One person can do it. I don’t have to have another tool to apply and press it, and my hands don’t get so tired and cold that you can’t apply it.”
“These products are also vapor-permeable, so I sell people on that too,” he continues. “Wind moisture will get behind your substrate at some point, and this allows air to move through it so that the OSB won’t get damaged.”
"I got away from Facebook and Instagram in college. I'd be looking at this random person's life and realized it was so dumb. I immediately deleted it. That was 8 years ago. I found so much more time in my life."
Young yet wise
Though Smith is a relative newcomer to construction at age 32, his approach to his work, and his life, is refreshingly sensible.
A self-starter who’s the first of his family to enter the field of construction, Smith rejects social media and all the baggage it carries, inspires that same healthy boundary with his five daughters, takes the time to enjoy his family in the present, and lives a lifestyle he desired while still staying within his means.
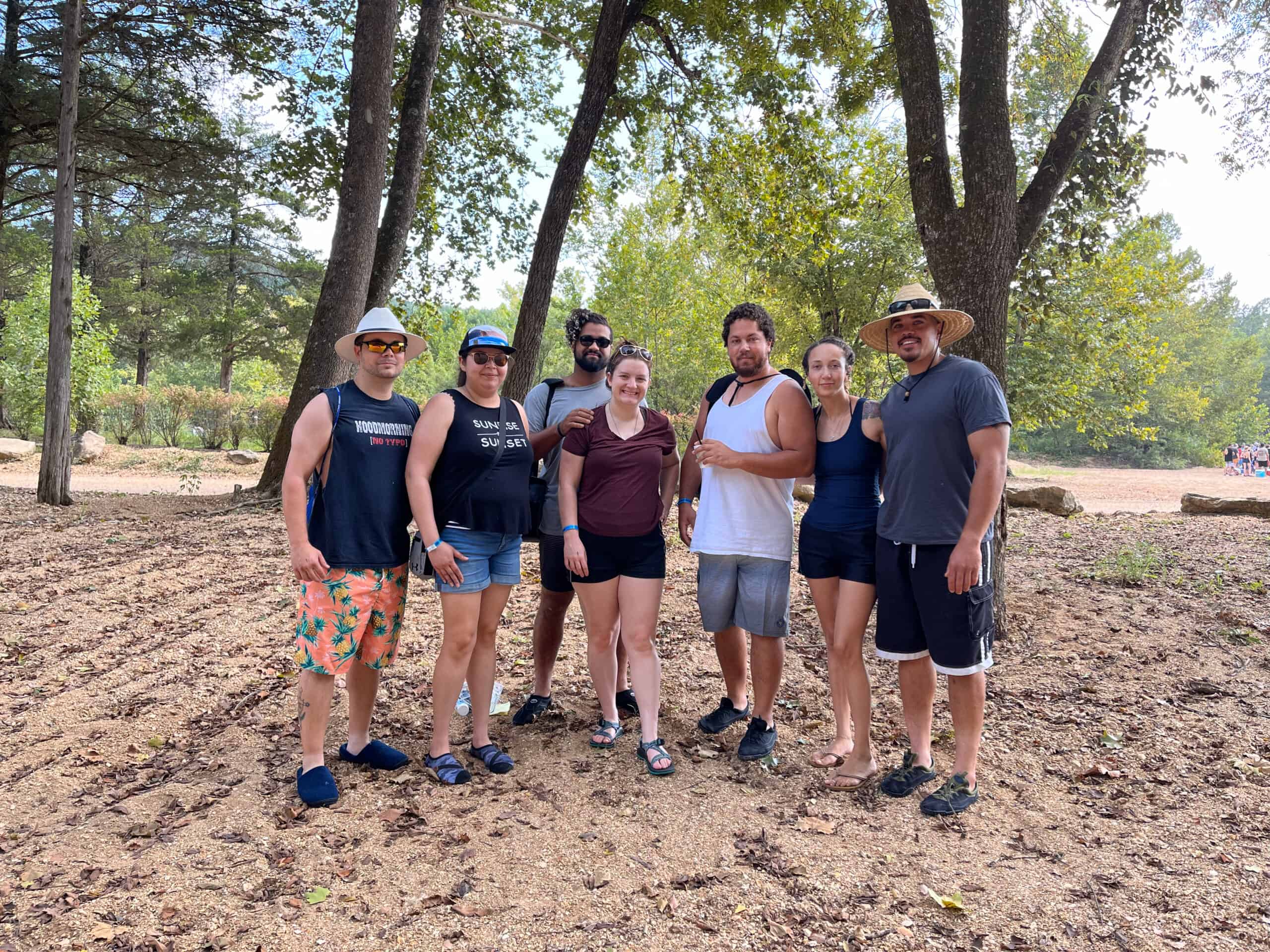
When he reflects on what he’s accomplished at his young age, he agrees he’s living the life of his design, but insists that his achievements aren’t out of reach for others.
“I wouldn’t say that my work is so phenomenal that nobody can ever reach it,” he says. “It’s good, but other people could do it if they were educated. I think it’s just the drive to learn that people are lacking.”
“My drive behind construction came when I bought my first home when I was 21 or 22. As I started getting into construction, I was upset that I spent so much on the home. They built this home for $50,000 and I bought it for $150,000. I realized I could physically do all of this. Then I just got fixated on wanting to build my own home. That was my dream to build my own home 100% by myself and be mortgage-free and away from debt. That was the biggest goal.”
“Sometimes people see the way I live now and think it’s kind of far-fetched. In my perspective, my life is not that flamboyant. We don’t have super fancy cars. We don’t have consumer debt of any kind. The whole point is that anybody can reach this but you have to educate yourself. I think that’s the biggest problem with our youth. They just don’t have the proper education to know what it is they want to do. I’m 32. What I hope people get from my life this far is to get out there and learn.”
How Landyn went from the Air Force to selling chips to owning his own construction company
