If you’ve ever heard the term densification, or concrete densifiers, you may be wondering what a densifier actually does to concrete, and why you would need one on your concrete floor?
Read our QA with Jeff Stepheson, Concrete Flooring Tech Specialist, for everything you need to know about concrete densifiers.
Q1: What is densification, and what does a densifier do to my concrete?
According to Stepheson, it all comes down to the chemistry of concrete.
“What makes up concrete right now is cement, water and aggregate,” he says. “The aggregate can range from sand to 1-inch rocks. What makes the magic happen is when you add water to cement and mix it, the process of hydration begins. Through the process of hydration, you get or calcium silicate hydrate gel, also known as CSH gel. That’s a very hard product that acts as the glue that holds concrete together. There’s another material produced through hydration that is a weaker, more porous material, and that is calcium hydroxide. In typical concrete, that’s produced at a rate of 160 pounds per cubic yard. That means there’s a lot of calcium hydroxide in the concrete.”
He explains that the chemical reaction that occurs when you introduce a silicate (via a densifier) to calcium hydroxide in concrete, actually changes the calcium hydroxide into the CSH gel. It’s what makes concrete such a durable and resilient material.
“By introducing a silicate densifier to the slab, you’re changing the weaker, porous material within the slab into a hard, binding product that makes concrete so good. That reaction is permanent. You cannot undo it. Since we’re introducing the densifier at the surface where all the wear from foot traffic happens, we’re tightening the cement matrix. Those voids with the weaker calcium hydroxide are now full of very hard CSH gel. It becomes a tighter, denser surface, which is why we call it a densifier.”
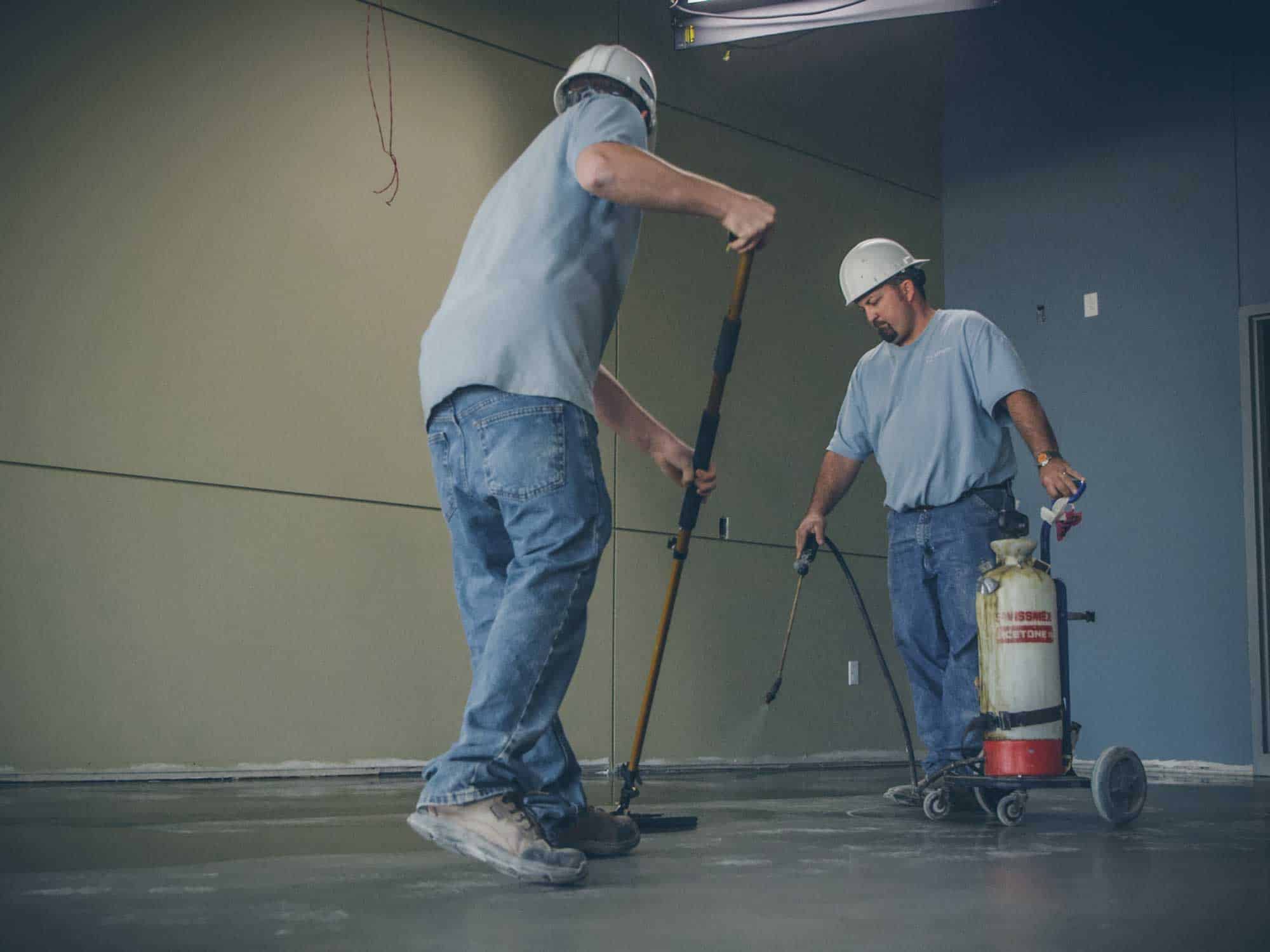
Q2: So, what would happen if I don’t densify my concrete?
“One of the reasons we like to densify with polished concrete is it gives you a tighter matrix at the surface that’s able to hold that polished finish you’ve created for a longer period of time. Without densification, the slab will be somewhat weaker, and it won’t be able to maintain the level of polish that you’ve created with your diamond grinding.”
Stepheson adds that many owners and contractors choose to apply a guard to add stain and water protection after densification is complete.
“The concrete is still porous,” he says. “We’ve made chemical changes to it, and we’ve strengthened it, but we haven’t made an effort to keep anything out of it. Densifying a concrete floor means there’s less space for things to get into, but it’s still a sponge. Just a much denser sponge.”
In a grocery store, for instance, a dropped jar of pickles could leave stains on polished concrete that are very hard to remove due to the acidity of the pickle juice.
“Concrete is very alkali,” Stepheson says. “It’s very high on the pH scale, so acids are very damaging to concrete, and we want to protect against those.”
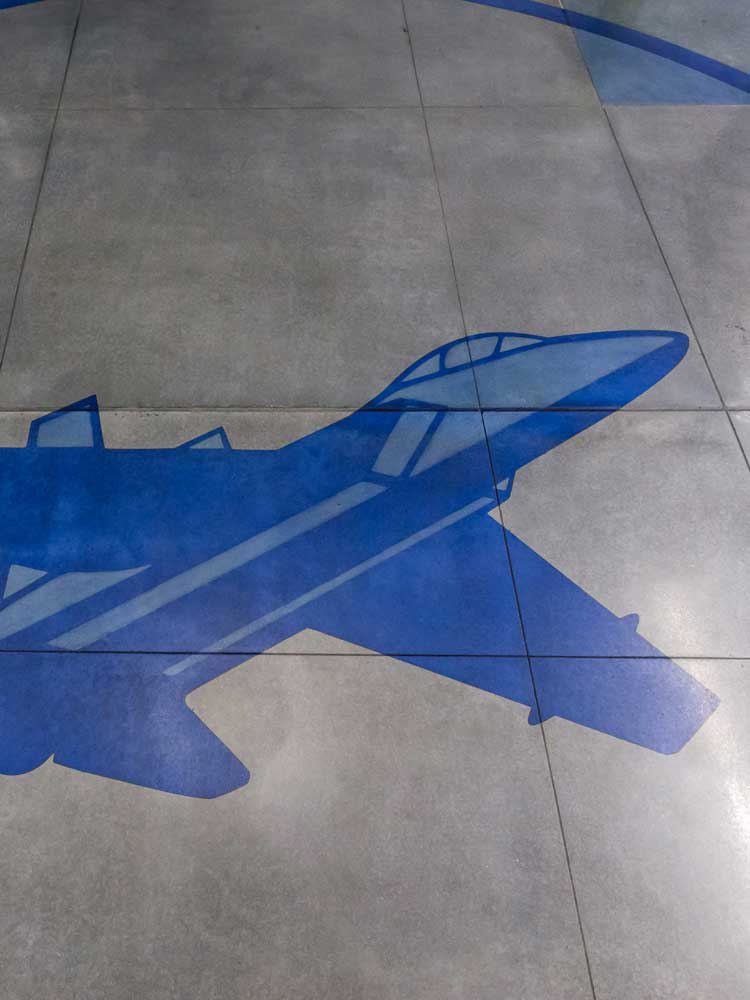
Q3: When should I densify concrete?
Unfortunately, there’s not a straight-forward answer to this question. “It depends,” Stepheson says.
The reason why it’s a hard question is that a densifier needs calcium hydroxide to be present in the concrete in order for it to do its job. Sometimes, that means you have to wait until calcium hydroxide forms. When does that happen?
“Calcium hydroxide forms pretty much immediately when you mix the water with cement and put it down,” he says. “There’s some amount of calcium hydroxide there, but if you densify too early, you may not achieve enough reaction to get the desired results. There are times you want to wait a certain amount of time to ensure you have enough chemicals to react with one another when you densify.”
For a typical customer, he says densification usually happens as part of the polishing process where curing isn’t a concern. In this case, the question of when to densify depends on the slab.
“If it’s a good quality, maybe a 3500- to 4000-psi mixed design, which is typical in commercial spaces, and it’s been cured properly, you can generally apply the densifier once you begin your resin steps, also called polishing steps. In most cases, densifying around 200 grit is pretty standard.”
(With resin steps or polishing steps, you start grinding with rougher grits (the lower, the rougher), then honing with the middle grits, and finally polishing with the fine grits. Grit sizes go up as you get closer to completion.)
“You’ve done your initial grinding, you’ve done the hard work of rough cutting of the surface. You don’t want to strengthen the slab before you do that. You want to get to the level of aggregate exposure and flatness of floor where the grinding is as easy as it’s going to get.”
Stepheson adds that if you’re adding color to the slab, he advises in the majority of cases to apply color at around 400 grit, then densify after the color is applied.
“Densifying should take place after color is down to help lock in that color. Also, if you densify before you put color down, you could be tightening the matrix up and not allowing as much color penetration as you’d like.”
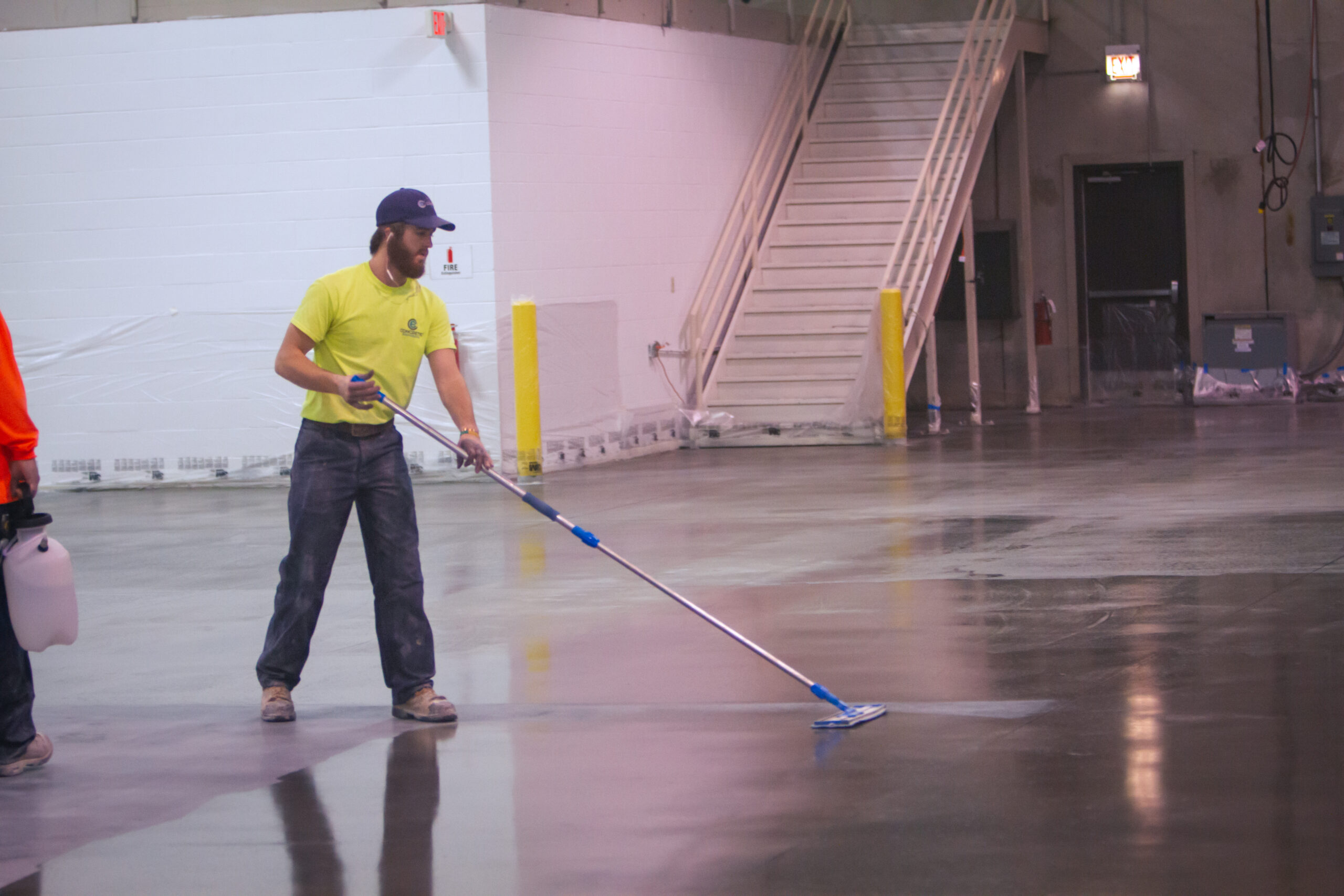
Q3: How do I apply a densifier?
After the nuance that goes into deciding when to densify, we have some good news. The “how” is much simpler.
“In the polishing process, generally, a lithium densifier is applied with a weed sprayer and followed by a microfiber mop to even out the coverage.”
While there are several different types of densifiers with varying chemical makeups, Stepheson says that lithium densifiers (such as Consolideck LS) are the most popular for polishing concrete because there’s no residue to remove, it’s very fast and you get a good reaction during the polishing process. He says other types of densifiers are used to achieve different outcomes. That includes Consolideck LS/CS, which is formulated to dustproof concrete floors and is popular in warehouses, distribution centers and other industrial spaces, and Blended Densifier, which is an ideal option for type 1L cement, or Portland limestone cement.
One rule of thumb he’s acquired over his 36 years in the industry is when applying a densifier, keep the slab visibly wet for about 10 minutes with no puddling.
“If you apply a densifier, and it’s dry in 10 seconds, you need to apply more. Continue to apply densifier if you notice it’s drying out.”
Another note of caution that Stepheson gives to customers is due to the fact that densifier applications can change the appearance of the slab to some degree. For this reason, it’s important to protect any surrounding workspace concrete that is not to be treated. If someone walks over an area where the densifier is still wet, and then walks over an untreated area of concrete, that footprint can be there forever.
Do you have more questions about concrete densification or another part of the polishing process? Get in touch with your local rep or technical sales rep, or give PROSOCO a call at 800-255-4255.
PROSOCO's densifier options
