The harmful nature of salt
Every winter, municipalities, homeowners and facility managers use salt to de-ice concrete streets, sidewalks, driveways, bridges and parking garage pillars. This salt, however, can lead to serious problems on concrete and exterior hard surfaces: Cracks, spalling and deterioration. Not only is salt artificially added to our outdoor spaces in geographic locations with cold winter climates, salt is also a natural issue in coastal regions where the air has higher salt content.
Salt-related deterioration is easy to spot on concrete. Given its porous nature, concrete absorbs water easily. In cold temperatures, water on roads and driveways turns to ice. Calcium hydroxide in concrete reacts with the calcium chloride in salt, forming calcium oxychloride (CAOXY). When it forms inside concrete, the crystals expand, causing damaging internal cracks and ultimately crumbling and surface flaking called spalling. This damage is amplified when salt lowers the freezing point of water and increases the pressure of frozen water, causing the effect of a freeze-thaw cycle. When ice melts, it carries a higher percentage of water than normal. In low temperatures, this extra water adds even more ice to the concrete when refreezing, and hydraulic pressure to the concrete.
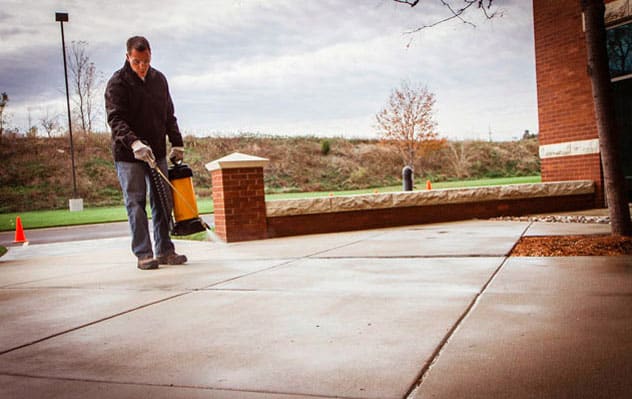
Rock salt (sodium chloride) accelerates the deterioration caused by winter's freeze-thaw cycles and shortens the lifespan of your concrete and even asphalt, yet it is the most popular deicing product in use.
Fresh-poured concrete has a higher water content and is even more susceptible to rock salt damage. You need at least a 30-day span between winter and the day your concrete driveway is poured.
While many might say to use alternatives, including snow blowing, shoveling, heated driveway systems or snow melting mats — these alternatives aren’t scalable and therefore not practical for commercial or municipal applications.
Can Surfaces Be Protected? Yes…
Instead of allocating massive funds in the annual cleanup and repair of salt damage, there is an effective family of products that provides a protective treatment to sidewalks, driveways and even concrete columns in a parking garage.
For example, PROSOCO’s Saltguard can last up to 10 years or longer, much longer than existing solutions that must be applied annually.
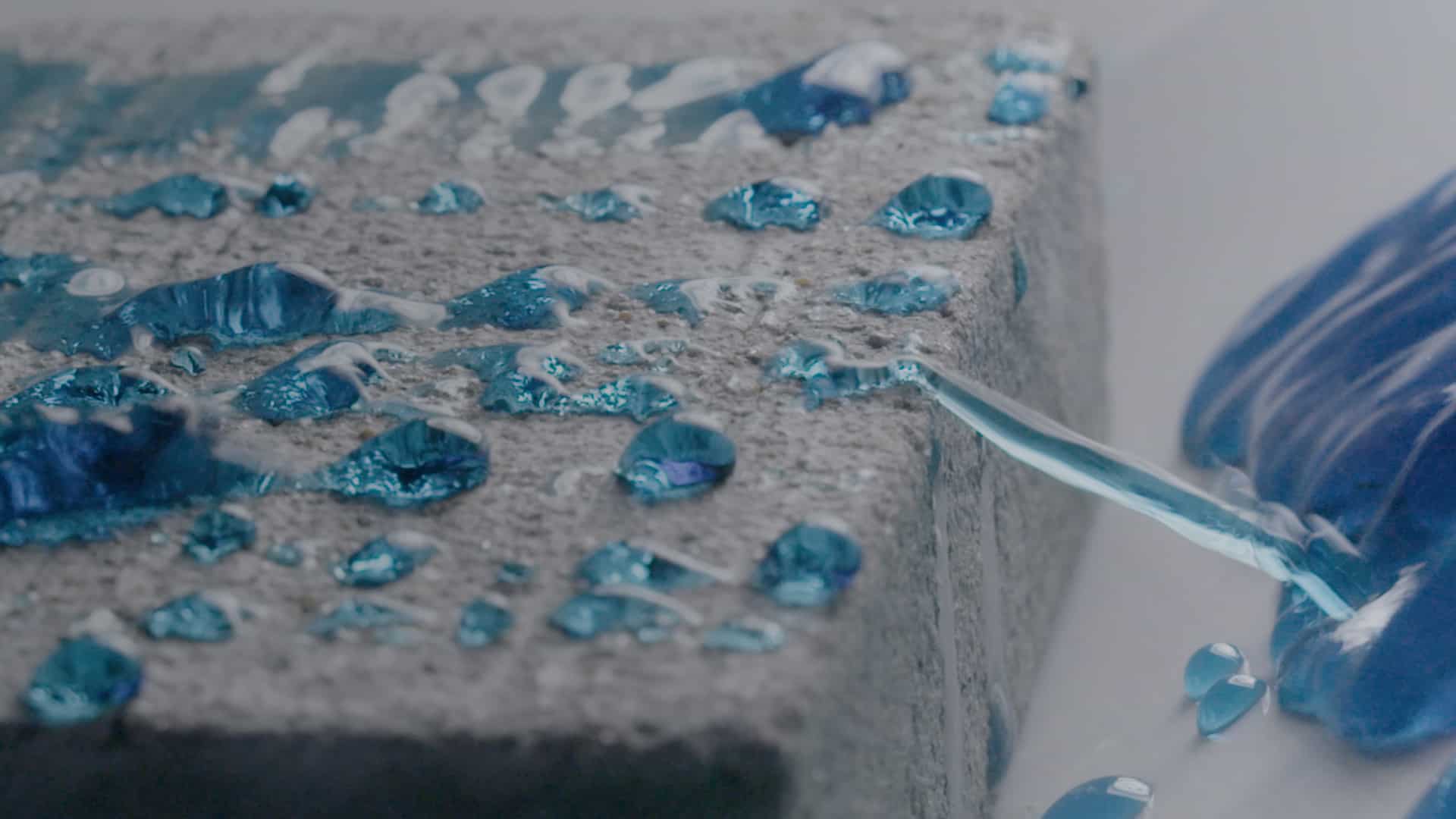
Timing is Everything
Late summer through early fall is ideal for applying Saltguard, at temperatures between 40−90°F. In many geographic areas, there is only a small window of time where the temperatures are ideal. To protect these surfaces against the damages of salt and freeze-thaw cycles, PROSOCO offers three variations of Saltguard. The original Saltguard is a solvent-based, silane/siloxane water repellent and chloride screen for concrete and masonry. It protects horizontal and vertical surfaces from moisture intrusion and chemical attack, reducing rebar corrosion and surface spalling.
Saltguard WB is a deep-penetration water-based formula, safe for use in all VOC-restricted markets. It penetrates deeply and is low-odor and alkaline-stable, it reduces rebar corrosion caused by salt content in moisture, especially in coastal regions, and is often used residentially for garage floors, sidewalks and patios.
The most recent addition to the Saltguard family is Saltguard VOC, a new solvent-based formula that’s compliant for most VOC-restricted markets. A water repellent and chloride screen for concrete and masonry, including concrete blocks, sidewalks, tile and brick pavers, it is compliant for use in VOC-restricted areas.
Saltguard’s price tag of between $50 and $70 a gallon makes it an extremely popular solution for both commercial and residential applications, especially given its long-life—protecting masonry and concrete surfaces for up to 10 years or more, depending on use and exposure.