A new milestone inspection law in Florida is leading to assessments for condo owners to cover repairs. But some are spending more money than necessary. Others are funding repairs that are unlikely to perform when the next tropical storm or hurricane hits. We talk with two professionals who believe – in many cases – there is a more economical and effective solution.
All up and down the U.S. East Coast, condo owners, developers and owners-associations are watching to see how their counterparts in Florida respond to a new Florida State Senate Bill (SB 4-D) requiring condo buildings three stories and higher to be inspected every 10 years starting when they turn 30 years old. (For condos within 3 miles of the coast, these Milestone Inspections start when condos turn 25 years old and recur every 10 years thereafter.)
In a state with 8,436 miles of shoreline and 1.5 million condominiums, more than half of which are 30 years or older, the rule affects thousands of Florida condo owners and construction professionals – with the most immediate attention paid to the repairs inspectors say are required to meet structural standards of safety.
Who foots the bill is the owners – by way of assessments handed down by condominium owners associations (COAs). A repair bill in the millions, say, for an entire recladding of a building, could mean hundreds of thousands of dollars for each individual condo unit when divided up equally amongst owners.
In many cases, owners who can’t afford to pay their share are left with no choice but to sell – both their unit and their dreams of retirement, or a source of retirement income through short-term renting.
“Ripping off perfectly good materials”
Florida condo owner Ron Tatley, who works as a Building Envelope Specialist for PROSOCO, is following these developments with a growing and urgent need to broadcast his message that – in many cases - the assessments handed down by COAs are costlier and more invasive than necessary. He knows a better way.
“All the work was unnecessary. That’s what’s happening with the condos and engineers in Florida. People get paranoid.”
“These associations have to rip off perfectly good materials, and they’re being replaced with poor materials,” he says. “They’re ripping out perfectly good sliding glass doors and windows, and replacing them with OK windows and doors, but the installation is poor.”
In the case of many direct-applied stucco buildings, they’re jack-hammering off perfectly good stucco, Tatley says. “The noise is insane on concrete buildings,” he says. “On one condo on the gulf side, three crews were jack-hammering day and night to get it all off by Spring Break.”
The tragic realization for Tatley was they didn’t need to jack-hammer the stucco at all.
“Only isolated areas were delaminating,” Tatley says. “They could have pinned it off, retained the existing stucco, removed the paint, and gone over it with Cat 5 and StuccoPrime, which is much easier. It’s less expensive, much faster and creates minimal noise. People wouldn’t have had to vacate.”
If condo owners live in their units part-time, and rent it out part-time for seasonal income, they’re faced with a double-whammy: pay for the repairs, and lose rental income if the building can’t be occupied during the repair.
“A lot of the condos down south are seasonal weekly rentals, so they’re facing the same thing,” Tatley says. “They won’t be able to rent them out if they’re going to be repaired.”
It’s simply a bad deal for individual owners.
“When condo HOA assessments come in so high and homeowners are forced to sell, developers buy up all of the units,” Tatley says. “Then they rent them back to the original homeowners. Once a condo building is converted into rental units, the building is no longer subject to Milestone Inspections.”
What this means, Tatley says, is that the original homeowner gets to stay in their unit, but they lose the seasonal rental income and growing equity they’d enjoyed when they owned the unit. Even worse, essential repairs may be further delayed.
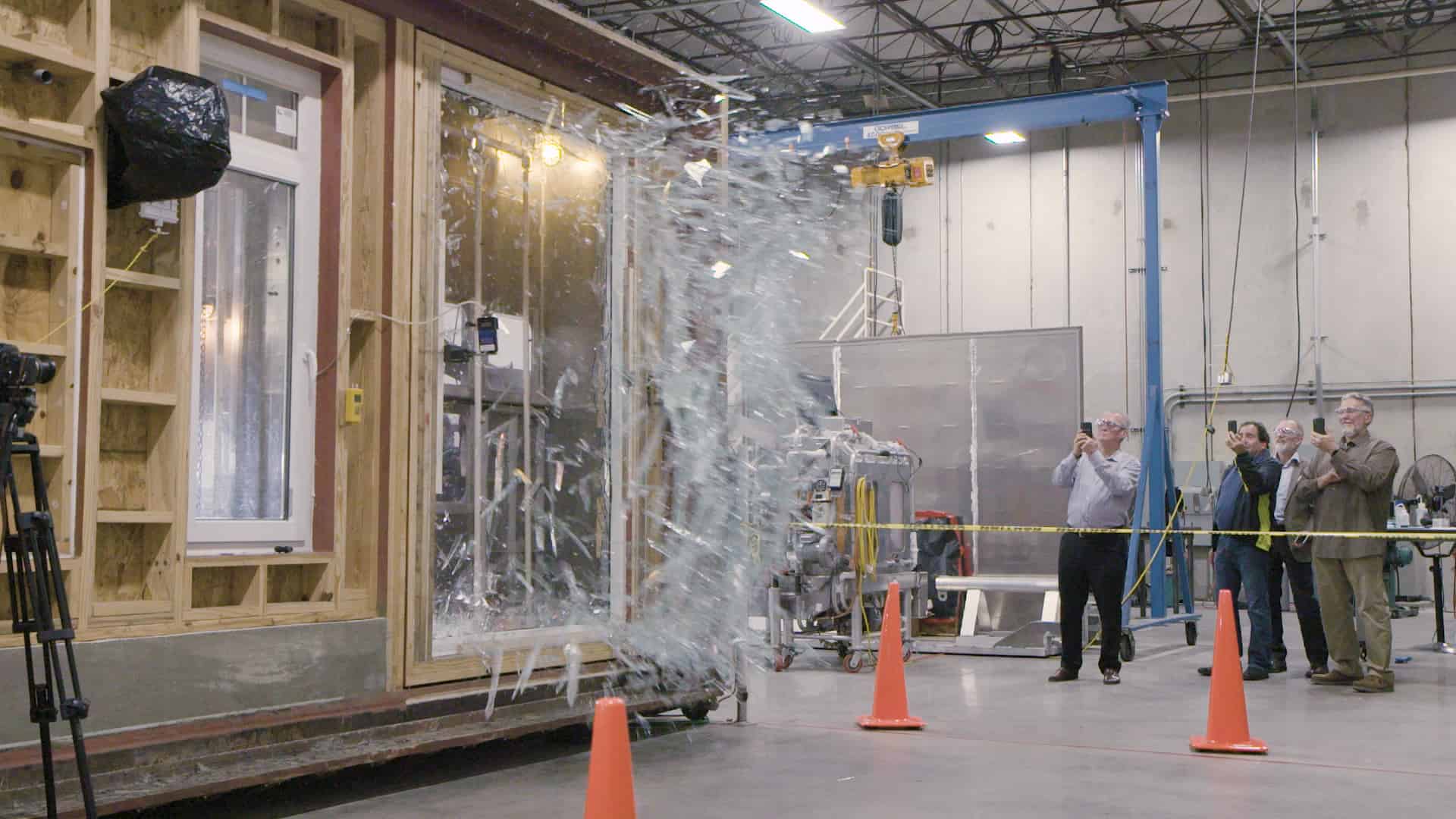
Tatley realizes he needs to get his message in front of several people – the engineer who performs the inspection, the property manager who signs off on the repairs, the contractor who completes the work, the owners who want to stay in their homes, the legislators who enacted the rule -- and anyone concerned about life safety.
But Tatley is confident that once people hear his message and see his test chambers that simulate severe weather conditions on wall assemblies, they’ll see the light.
On one building he assessed in his prior role with restoration contractor Tatley-Grund, the inspection report called for $1.6 million in repairs. When Tatley got involved and hired a new building envelope consultant, together they got the repair bill down to $60,000.
“All the work was unnecessary,” Tatley says. “That’s what’s happening with the condos and engineers in Florida. People get paranoid. People may not know what they’re looking at when they see the inspection report, and the property managers signing off on the repairs want to make sure they’re doing the right thing.”
“Once I got my hands on a true STP, it was like magic. It was amazing. I couldn’t believe something out there checked so many things on the wishlist.”
“The mistakes are rampant. We’re forgetting lessons learned.”
The reason Milestone Inspections in Florida are targeting condos built in the late 1990s and early 2000s is because of the way they were built, says PROSOCO CEO David Boyer. Looking at the builds of that era, he says, “Takes us back to simple, low-cost, barrier wall assemblies that pre-date building science as we know it today.”
Those barrier walls are a zero-tolerance system made of a single element, Boyer explains. “Most feature limited flashings, little-to-no overhangs, no rainscreens, and ‘affordable’ windows and doors. If a seal, gasket, or external coating fails, water will enter the building.”
Combined, all these factors increase the likelihood that water will enter these simple barrier wall assemblies and not be allowed to escape. An overwhelming majority of the damage Boyer sees today is caused by moisture that can’t dry out and can’t get out of the wall.
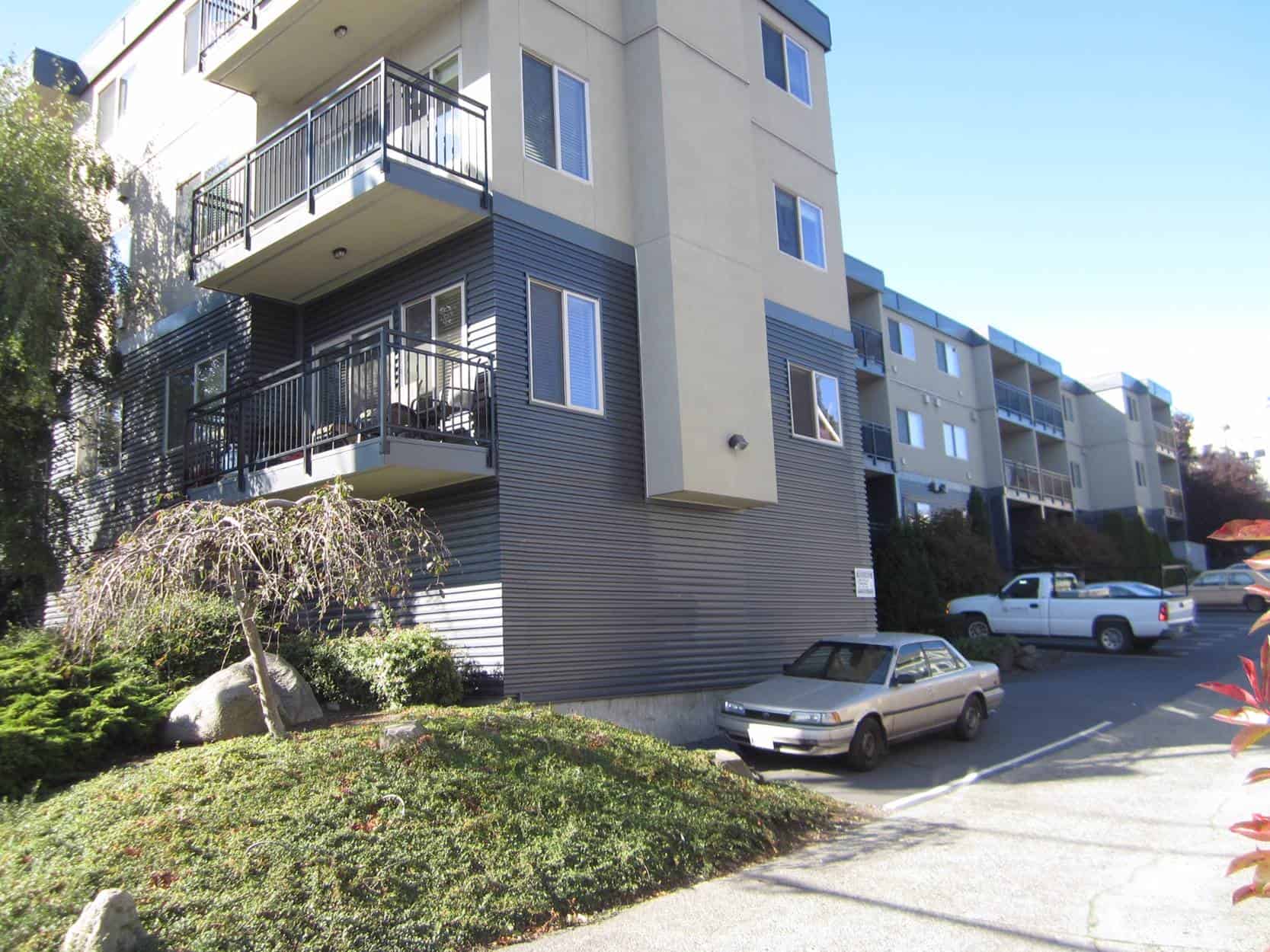
“Back then, we had this false belief that the technology, the new chemistries and the elastomeric coatings and sealants were so good, that we could keep Mother Nature outside,” Boyer says. “When we realized they couldn’t, that gave birth to energy-efficient designs, rainscreen assemblies, and all the things we realize today are needed to make buildings survive in severe climates.”
Boyer and Tatley both recognize what’s happening in Florida because they’ve seen it before, in Seattle. Lessons learned from the notorious leaky condo crisis on the West Coast, which began in the late 1980s and progressed all the way from Vancouver, British Columbia, down to Southern California, have sorely been forgotten.
“This industry is ... doing rinse-and-repeat repairs while failing to look deeply enough to realize this building is in jeopardy.”
“Many of today’s building science pioneers, including Ron Tatley, took part in studies that identified the inadequacies of simple barrier wall assemblies and spurred evolution of the modern, energy-efficient drainage wall assembly,” Boyer says.
Today, Tatley and other members of the building science community know better about building methodologies for long-term durability in extreme climate zones, but Boyer is still seeing many incorrect repairs on Florida condos that were built 25 to 30 years ago.
“They’re relying upon another coat of a surface-applied elastomeric coating or paint, and new sealant, and they’re not fully routing up joints to restore the barrier that had failed,” he says. “You’re seeing that over and over.”
“The leaky condo crisis on the West Coast and the class-action lawsuits from the 1980s and 90s are two major industry events that shaped the path forward, and they shape so much of what PROSOCO does today. We’re reteaching those lessons in Florida right now. The mistakes are just rampant.”
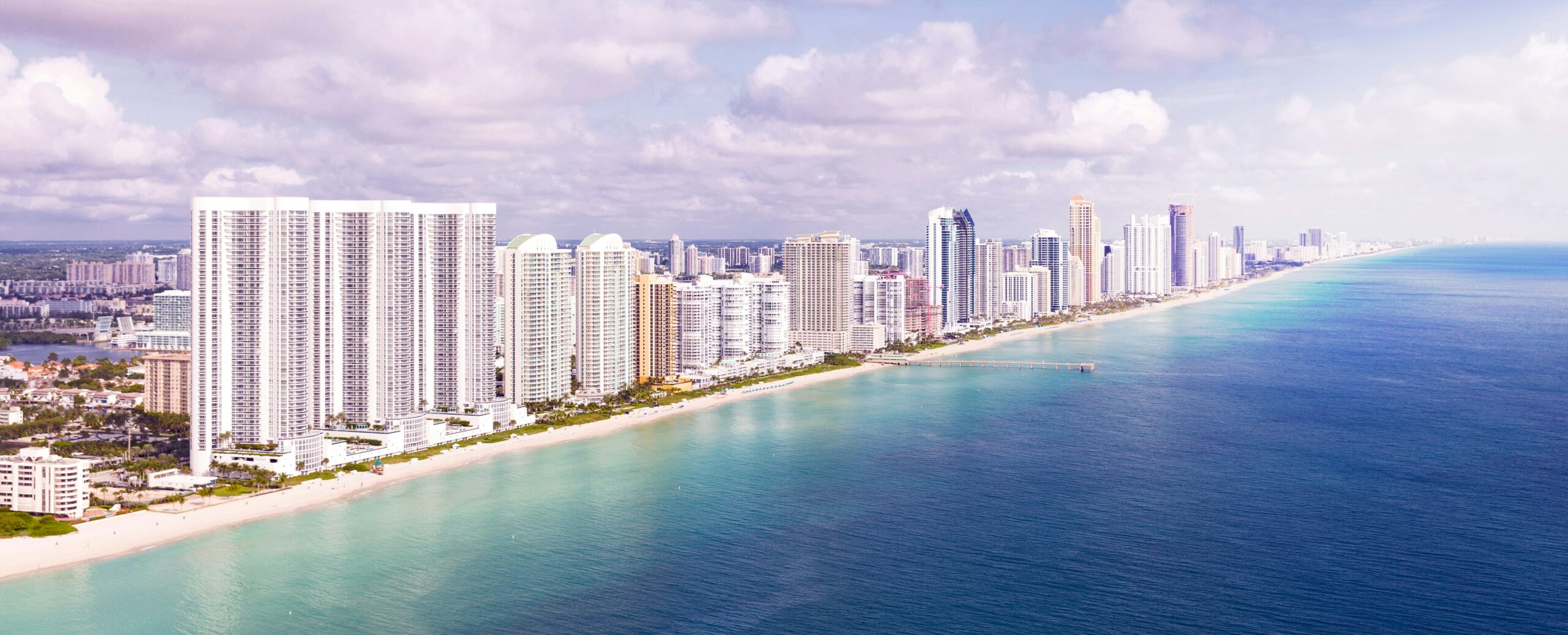
For one thing, an elastomeric paint or coating is not breathable, meaning that any vapor transmission initially present in the wall assembly will be diminished with each additional coat of that material. Also, sometimes joints are not being repaired with new sealants, leaving a big weakness in structures’ walls.
“They’re putting band-aids over the wounds that these buildings have suffered from since they were built,” Boyer says. “They’re grabbing at straws and spending available resources for condo associations according to what they can afford, with no attendance to what they need to address first.”
Boyer remembers one 12-story condominium he saw that was so structurally compromised, it shouldn’t even be occupied.
“This industry is built up around surveying the buildings and doing rinse-and-repeat repairs while failing to look deeply enough to realize this building is in jeopardy,” he says.
Stay calm and heed the testing
The tendency to panic given these circumstances is understandable, but Tatley stresses the importance of keeping a level head, because panic is what’s leading many COAs to rashly say yes to repairs that Tatley believes - in most cases - are unnecessary.
“Each building has to be looked at individually. For those finished with direct-applied stucco, the use of anchors, as opposed to total stucco removal, needs to be considered,” Tatley says. He recommends an anchor called a Stucco-Tie, which mechanically reconnects exterior stucco finishes to backup materials. This eliminates the cost and inconvenience of removing an entire stucco façade via jack-hammer.
“When assessments come in so high and homeowners are forced to sell, developers buy up all of the units. Once converted into rental units, the building is no longer subject to Milestone Inspections.”
“You can remove windows and reinstall them with FastFlash and get a waterproof window,” he adds. “There’s so many different variables, including the variety of building materials common in Florida like stucco, EIFS, solid wall, and cast-in-place construction, but we could fix 95% of everything out there.”
Boyer seconds Tatley’s recommendation of installing Stucco-Ties into existing stucco; removing the elastomeric paint; waterproofing with FastFlash, Cat 5, and AirDam; applying a “link coat” of StuccoPrime; and applying one additional finish coat of an integrally colored stucco.
The important distinction about a coating like Cat 5 (as opposed to the non-breathable elastomeric coatings and paints previously mentioned), is that Cat 5 is breathable and vapor-permeable, meaning it won’t trap water in the wall. Boyer adds that because Cat 5 is hidden behind an additional layer of stucco, it’s not exposed to the powerful UV of the Florida sun.
“It adds a level of redundant protection against Mother Nature while saving on the cost and inconvenience of complete stucco removal,” he says.
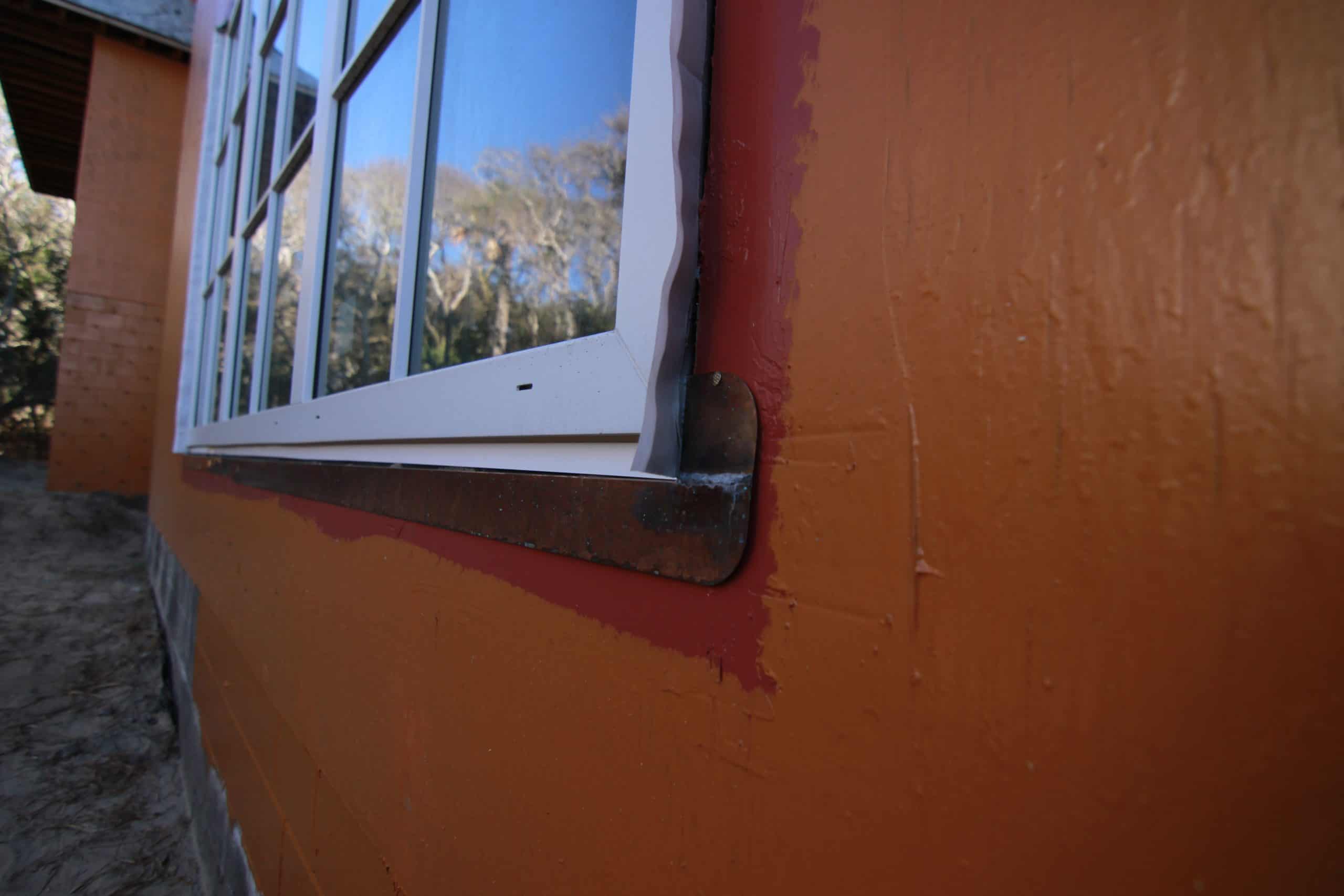
Seattle 2.0 = Florida
The reason Tatley is so knowledgeable about the waterproofing qualities of FastFlash is that he’s the person who developed the technology. The origin story of FastFlash, the first fluid-applied flashing membrane with silyl-terminated polymer (STP) technology on the market, intersects with the story of Tatley’s test chamber in his shop in Santa Rosa Beach, Fla. -- the very test chamber he says holds the clues to building better, more durable, and more resilient wall assemblies to stand up to the most severe weather conditions imaginable.
It all started in Seattle, on a Tatley-Grund project with brand-new, pre-purchased sliding glass doors that immediately failed.
“We were just installing the specified materials, and we quickly learned that the specified materials did not meet exposure requirements,” Tatley says. “We were installing something that failed miserably and wasn’t going to survive. That’s when we started building the test chambers.”
A large simulator of weather conditions up to a Category 5 hurricane, including severe winds and tidal surges, the chamber tests various wall assembly components and configurations under those conditions.
Boyer says it’s no exaggeration to call the test chamber an absolute game-changer.
“It emulates the conditions you’re trying to build against,” he says. “It can measure the rate at which drying occurs. We’ve brought world-renowned building scientists here to see what we’re doing and to watch a chamber demo. One said, ‘You’re the first people to do this.’”
The chamber has been busy since its inception in the early 2000s. It’s the reason why FastFlash exists.
Using data acquired from the test chamber, Tatley and his business partners, Stace Grund and Tom Schneider, created a “contractor’s wishlist” of criteria they desired out of a fluid-applied material to waterproof rough openings of doors and windows – and the result was FastFlash.
“I tested a lot of fluid-applied products, and they all had problems,” Tatley says. “That’s why I went to STP (silyl-terminated polymer) technology.”
“I tested a really cheap version someone made, and it didn’t pass my testing. It wasn’t an STP. Once I got my hands on a true STP, it was like magic. It was amazing. I couldn’t believe something out there checked so many things on the wishlist. Most of the others got to 50%, if we were lucky.”
One of the most important qualities of STP technology (found in FastFlash, Cat 5, AirDam and Joint & Seam Filler) is that it can be applied to damp surfaces and even while it is raining – a big advantage in rainy regions like the Pacific Northwest and Florida.
Today, the chamber is hard at work in Tatley’s shop, where he welcomes anyone interested in gaining a deeper understanding of how to make better buildings, and how to better address Florida’s growing condo crisis.
“Our condo’s handyman comes over regularly, and he’s just a brilliant guy,” Tatley says. “He knows so much about building science. He can learn more in two days than a building envelope scientist can in a year, just by what he witnesses here.”
“Now one of my goals is to get more building envelope consultants and engineers here. When we get them here to see the demos, it’s like a lightbulb going off. The test chambers give people confidence. That’s what they did in Seattle.”
Want to see the test chambers in person?
Come see our state-of-the-art test chamber, learn cost-efficient methods to repair failing condo buildings, and meet our knowledgeable staff of experts.
Sign up for our free test chamber event on June 10, 2025, in Santa Rosa Beach, Fla.