So many problems on buildings originate with water. If water gets inside a wall assembly and has no way to get out, it can cause all sorts of structural and surface damage, including stains, mold, and rot. Water repellents are an easy solution to keep water out of masonry, and the performance of your water repellent can depend drastically on its application – and whether it was done the right way. Here are some quick best practices to keep in mind before applying a water repellent to your masonry.
Get a clean start.
For starters, you want to make sure the substrate is clean, dry, and free from any contamination that may interfere with the water repellent.
“The last thing you want to do is protect stains on the wall too, as that will make them much harder to remove later on,” says Jake Boyer, PROSOCO’s Vice President of Sales. “In general, the substrate should look the way you intend prior to application.”
Apply it right.
Most water repellents, both penetrating and film-forming, have similar application methods. They’re commonly applied with a pump-up sprayer, a low-pressure diaphragm pump, or an HVLP (high-volume, low-pressure) airless paint sprayer.
Many manufacturers recommend applying the product from the bottom up in a saturating spray and an overlapping pattern to ensure full coverage. Most also call for two coats or at least one wet-on-wet coat.
Atomizing the product as you spray should be avoided, because it could result in either the carrier solvent or the active ingredients in the water repellent “flashing off” before it reaches the substrate. For this reason, low-pressure is also essential – typically no higher than 50 psi, Boyer adds.
For porous substrates, the product data sheet may call for a certain length (usually 4-8 inches) of run-down from the point of contact where the spray pattern meets the wall. The water repellent should be allowed to run down that length before absorbing back into the substrate.
“If it runs or drips further than that, you may need to brush or roll those drip lines out to avoid streaks,” Boyer says.
On more dense or smooth surfaces, it may be best to use just enough product to wet the substrate without creating any run-down.
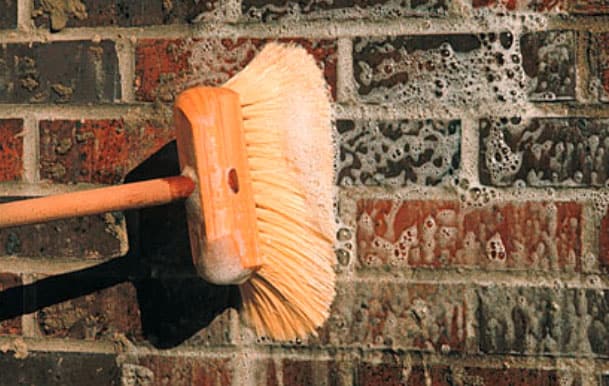
Follow directions.
It may seem like common sense to read the manufacturer’s product data sheet and follow application instructions to a T, but Boyer sees signs every day that suggest otherwise.
The product data sheet gives you the information you need to make sure you’re using the right application methods and techniques appropriate for your specific conditions.
Boyer adds that regardless of the substrate and product used, there is no such thing as a “maintenance-free” product or material. That maintenance can be significantly reduced by using the right product, but that product may still need to be reapplied at some point during its life. Consult the manufacturer to determine the expected life cycle and set a reminder to test the wall again when needed to determine if reapplication is necessary.
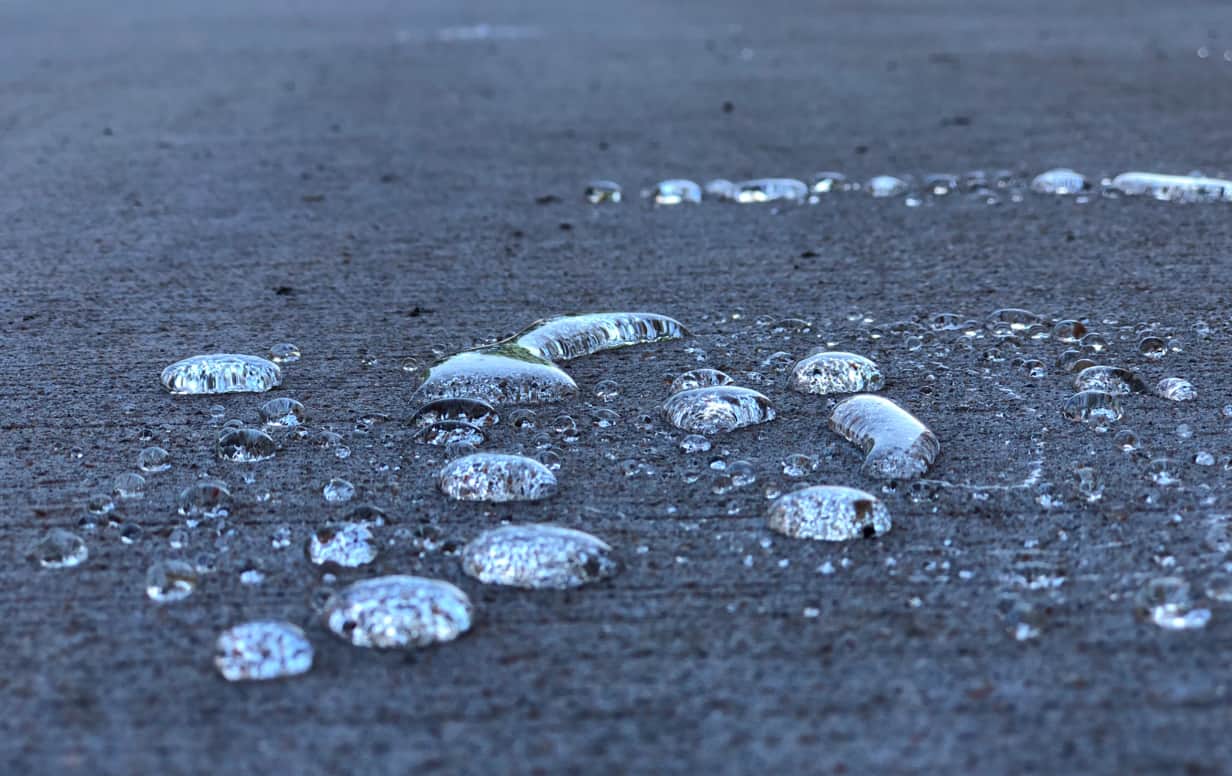
Manage expectations.
When it comes to your expectations of how long a water repellent will last, knowing the performance characteristics of each product type is the best place to start.
For instance, film-forming water repellents are typically the shortest-lived options because they sit at the surface where they’re exposed to the elements. In general, these can last anywhere from 1 to 5 years, Boyer says, but they may need to be stripped before reapplying.
On the other hand, if you’re working with a penetrating water repellent, the life cycle is typically a minimum of 5 years, and it can last up to 20 years or longer with the proper application.
“Managing expectations from the beginning is key to success because every situation is a little different by way of what a building is exposed to and the combination of materials used,” Boyer says. “The key to longevity is ensuring proper product selection, installation and coverage rates. Beyond that, think about where your project is located and the conditions your building will be exposed to as you set your expectations. If there’s heavy salt air or water, deicing salts, heavy vehicular traffic, or heavy UV exposure, you’ll want to select your product accordingly.”
PROSOCO offers these breathable water repellents
