The six-story, 50,000 square foot Bullitt Center is seeking to change how buildings are designed, built and operated. Its goal: to shift the benchmarks significantly forward for long-term environmental performance and energy efficiency, renewable energy and other green building technologies.
Seattle’s Bullitt Center seeks to be a “living building” -- one of the greenest, most energy-efficient commercial buildings on earth. The Bullitt Center is being constructed to meet the ambitious goals of the Living Building Challenge, the world’s most stringent criterion for sustainability.
A rooftop solar array will generate all the electricity the building uses. Its water will come from rain, and all wastewater will be treated onsite. The Bullitt Center’s design does more than meet the tough targets of Net Zero energy and water use. It’s being constructed without anything on a “red list” of commonly used construction materials; substances designated by the U.S. Environmental Protection Agency as harmful to living creatures -- including humans. Designed to maximize fresh air and daylight, the Bullitt Center will be living proof that buildings can be environmentally friendly, energy efficient, pleasant, healthy and sustainable. The Bullitt Center is expected to be completed in late 2012.
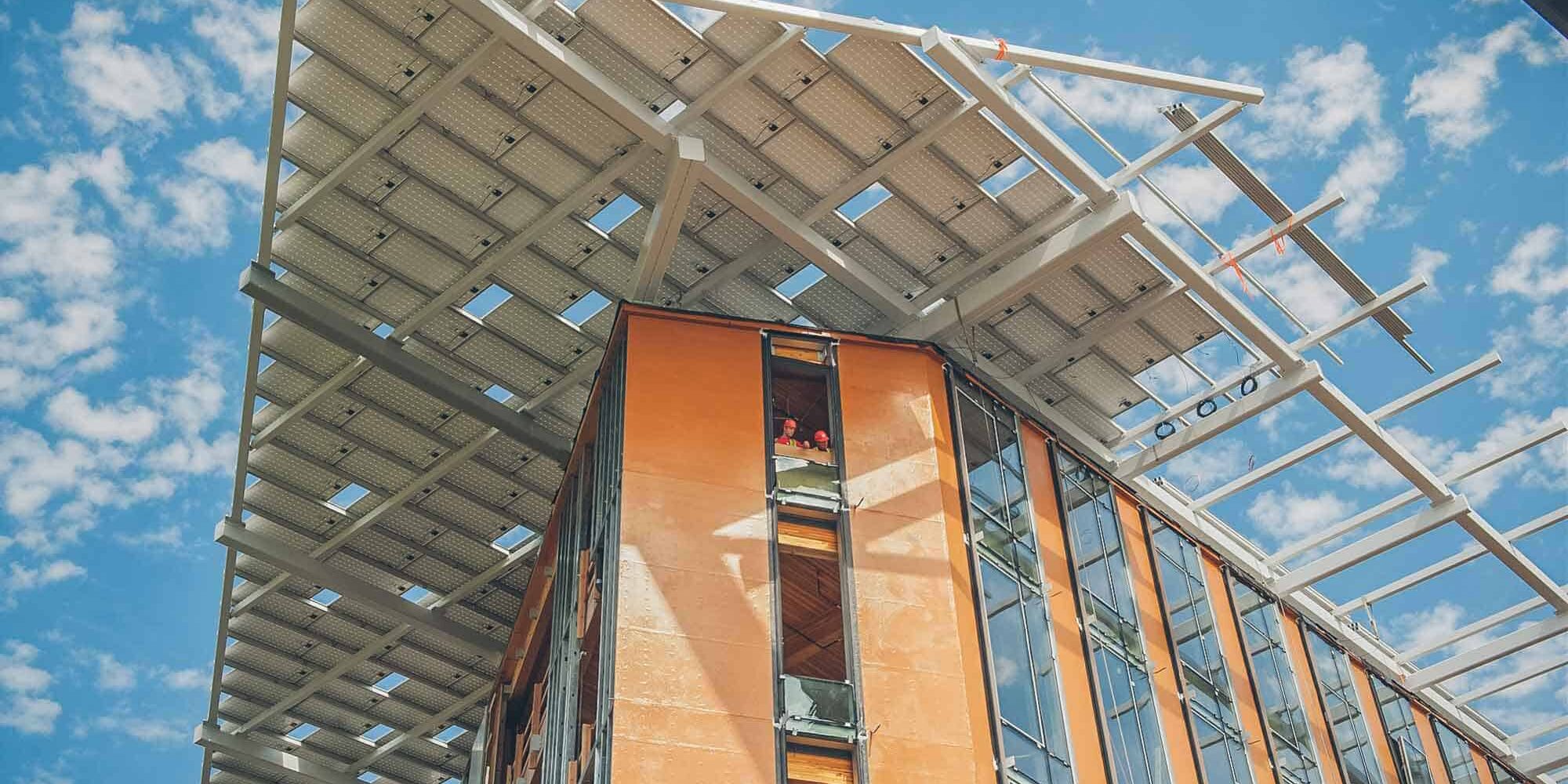
Net-Zero Energy Efficiency
Net-Zero energy efficiency means the building creates ALL its own energy. Energy drawn from the grid = zero. In a Net-Zero building, there is no energy to waste.
That means air leaks through the building envelope, which normally account for up to 40 percent of heating and cooling costs, cannot be tolerated. Bullitt Center builders chose PROSOCO R-Guard Air & Waterproof Barrier system from dozens of alternatives to do that job.
When we came across a company like Prosoco, who is prepared to take all of the phthalates out of their products, this was just a wonderful example of this theory of change that we have.
Denis Hayes
Bullitt Foundation President
Installed at the Bullitt Center by Katwall Inc., Seattle, Wash., the continuous, durable, vapor-permeable system contributes to energy efficiency by creating a continuous, unbroken barrier to the movement of air through the building envelope. The FastFlash system is tested and proven in weather from mild to Category 5 hurricanes – even before the building is clad.
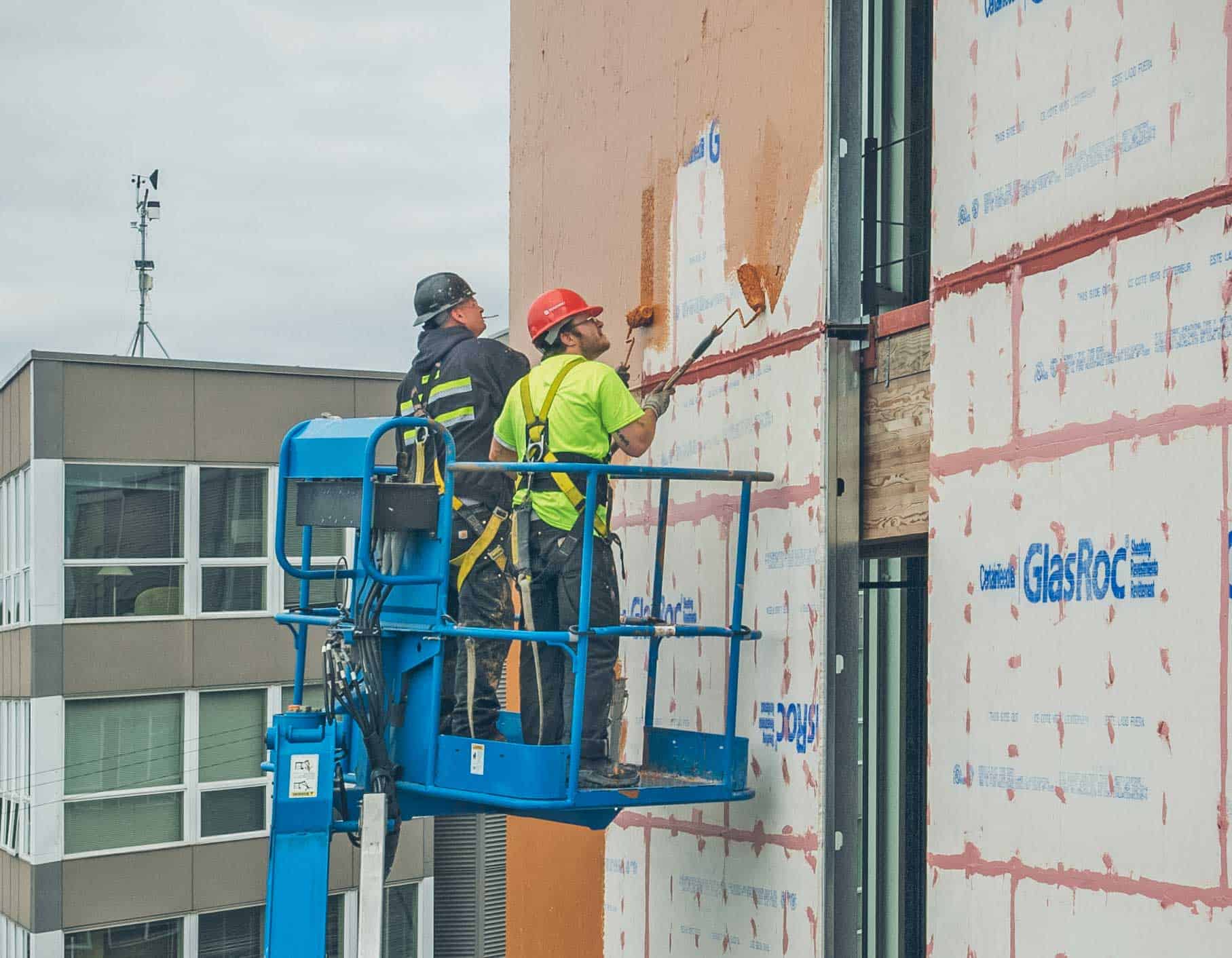
R-GUARD Air & Waterproof Barrier
Stopping air leaks through the building envelope is crucial to energy efficiency in all buildings, Net-Zero, Passive House or standard construction. The U.S. Department of Energy estimates up to 40 percent of annual heating and cooling costs result from expensively heated or cooled air leaking out through seams, joints, and penetrations, and around windows and doors in building envelopes.
How to install the complete R-Guard system

Peel and stick membranes can’t stop it, because they eventually delaminate, letting air through and letting in moisture. Fabric wraps can’t stop it because they rip and tear under wind loads during construction. Even the tiny staples used to fasten fabrics create air leaks. Along with peel and stick membranes, many vapor-impermeable fluid-applied membranes trap water in the walls and around rough openings. This speeds up the very deterioration the products are supposed to prevent.
The Bullitt Center’s builders chose the FastFlash system expressly to surmount these problems.
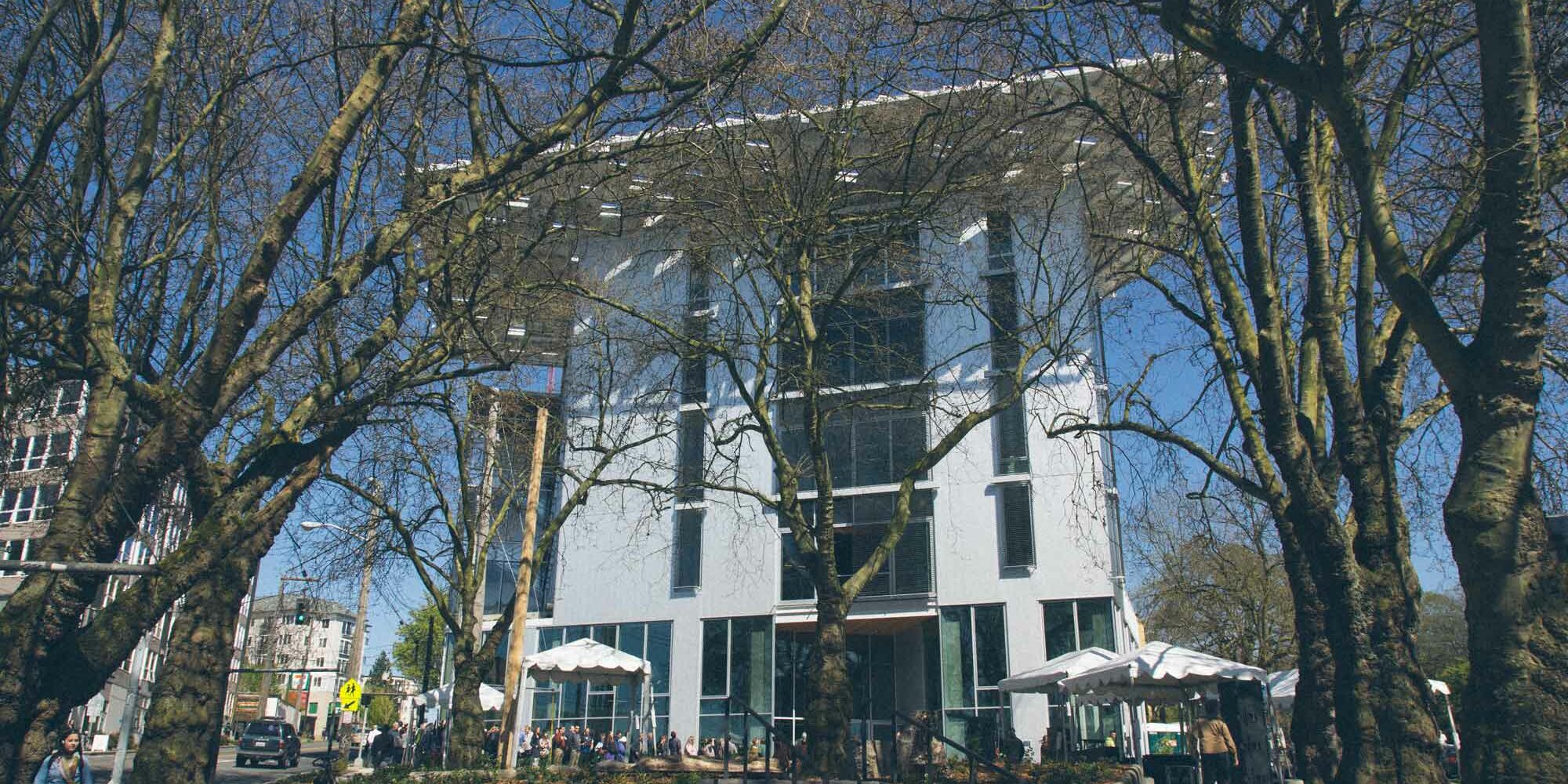
Supremely durable, yet simple to apply, the FastFlash system solves many other problems in addition to stopping air leaks at a level enabling NetZero energy-efficiency. Unlike other products that must be protected from rain while curing, the FastFlash system is instantly waterproof from the moment it’s applied.
Unlike other products, you don’t have to wait for raindampened surfaces to dry out before you install the system. Moisture accelerates FastFlash curing time. Because it’s vapor permeable, wet substrates underneath can dry out. And unlike other products, FastFlash doesn’t contain red-listed phthalates, classed as harmful air and water pollutants by the U.S. Environmental Protection Agency. In a construction industry ever-more conscious of environmental concerns, the FastFlash Air & Waterproof Barrier system complies with the Living Building Challenge - the most environmentally friendly standard ever created.
FastFlash Case Study: 10 Years of Proof
The environmentally friendly FastFlash Air & Waterproof Barrier System complies with the Living Building Challenge Red List requirements.
The project cannot contain any of these Red List materials:
- Asbestos
- Cadmium
- Chlorinated Polyethylene and Chlorosulfonated Polyethlene43
- Chlorofluorocarbons (CFCs)
- Chloroprene (Neoprene)
- Formaldehyde (added)
- Halogenated Flame Retardants44
- Hydrochlorofluorocarbons (HCFCs)
- Lead (added)
- Mercury
- Petrochemical Fertilizers and Pesticides45
- Phthalates
- Polyvinyl Chloride (PVC)
- Wood treatments with Creosote, Arsenic or Pentachlorophenol
Natalie demonstrates how to install FastFlash
