A Seattle building envelope consultant gives his observations on successful blower door tests.
We got the chance to speak recently with Denali Jones, a senior project engineer for the Seattle office of a firm called RDH Building Science.
Part of his job is conducting blower door tests for clients and helping project teams achieve their energy goals on buildings. As a professional who conducts roughly one blower door test a month and has completed hundreds over his career, he knows a lot about what it takes, and what it doesn’t take, to meet energy-based standards of airtightness in a building envelope.
“If it has to do with keeping the outside out and the inside in, we deal with it,” he said. “Anything related to the building envelope, whether it’s air barriers, roofing, insulation, all of it. Air barrier testing is a big part of that.”
In Seattle especially, air barrier testing has been keeping Jones busy, for more reason than one.
Not only does Washington state have an airtightness requirement (less than 0.4 cubic feet per minute (cfm) per square foot) built into its code, the city of Seattle has an even stricter code requirement of less than 0.3 cfm per minute.
Beyond this code-mandated focus on the airtightness of a building envelope, Washington state also introduced, in its 2015 code, an energy code requirement (Section C406) to include two out of eight different energy-oriented options on all new construction. Those include installing solar panels, improving daylighting controls, and adding insulation. Another option is to increase airtightness with an even lower threshold of 0.25 cfm per minute via blower door test.
Unless a client is aiming for that energy code option, or another energy-based standard like Passive House, Jones says he generally doesn’t do anything special in terms of detailing and specifying the air barrier. What’s more important is the installation.
“The level of QC (quality control) in the field is how things come together,” he said. “If we’re going for a higher standard, we might insist on a higher level of QC, a fully adhered system, and some interim testing in the field to make sure we’re on the right track.”
Because it’s concealed behind the cladding, the air barrier is almost completely installed by the time the blower door test is typically conducted, a point at which it would be difficult to go back and redo the air barrier.
Therefore, you really only get one shot at it, Jones said. “There aren’t many scenarios where you have an iterative process.”
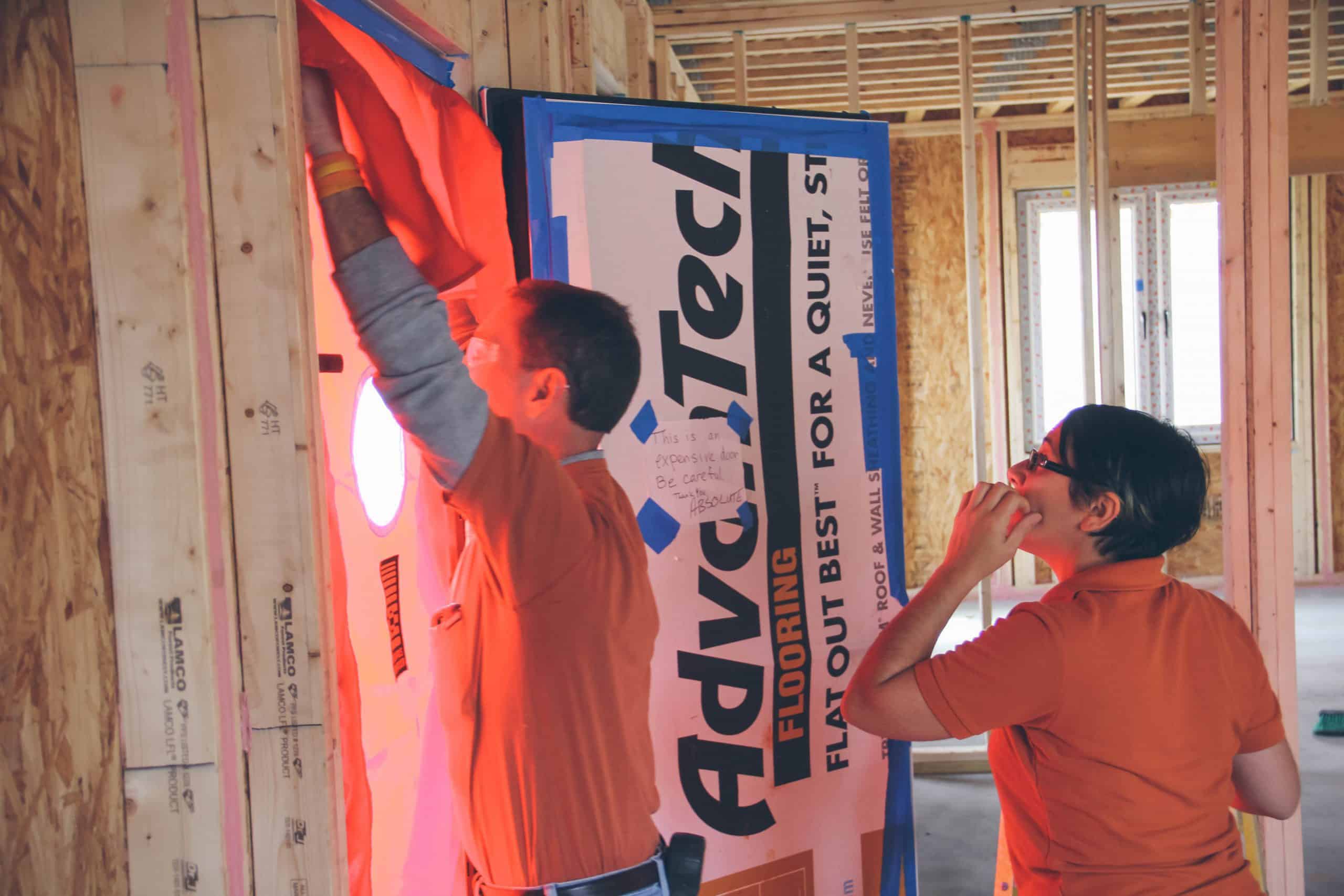
For those higher-achieving projects when it comes to energy, Jones takes special considerations when recommending products, systems and installers to his clients.
“Our role is to make sure that the owner and architect are making informed decisions about what they’ve specified and what they’re drawing, that they’re aware of the risks involved and the benefits,” he said. “That they get what they’re paying for. Not everyone can afford to build the best building every time, so it’s more about understanding where to save, and where it’s not a good idea to cut back.”
That all depends on the owner’s expectations in terms of durability and maintenance. For instance, how long do they want the roof to last?
“Some only want a 15-year roof, and some institutional clients might want a 40-year roof,” he said. “There are no hard and fast rules. You need to meet code and follow the standard industry practice, but some people might want to go above and beyond that, and some people don’t.”
While Jones has consulted on many projects wrapped in house wrap that have no problems passing their blower door tests, he uses a lot of PROSOSO R-Guard fluid-applied products because their STPE (silyl-terminated polyether) chemistry provides such a big advantage in a notoriously rainy climate like the Pacific Northwest.
“You can count on having rain most of the year here, and if you’re going to get a product to stick to wet substrates, it can be difficult,” Jones said. “STPE chemistry is really forgiving for damp substrates, whereas an acrylic would just run off the wall. It’s really impractical to try to install that in our climate. It’s too difficult to manage here without tenting the whole building, which is a big added cost.”
With house wraps, or sheet goods, you’re also leaning a whole lot harder on the quality of the install.
“You’re relying so much on a guy in the field taping seams together,” he said. “It can be pretty finicky to get it right.”
“STPE chemistry is really forgiving for damp substrates, whereas an acrylic would just run off the wall. It’s really impractical to try to install that in our climate.”
Airtightness isn’t the only consideration when Jones and his colleagues recommend a product for an air barrier.
“We also look at compatibility with sealants, does it seal around penetrations, does it seal around windows and doors,” he said. “There are a thousand different interfaces where you’re going to have to seal to that membrane.”
A fully adhered air barrier can be more important on multifamily construction due to the sheer number of penetrations through the air barrier. For example, a multifamily structure has an exhaust fan in every single unit, whereas a commercial office building has just one central HVAC and one or two points of penetration, Jones said.
“Just by that nature, multifamily construction tends to be a bit leakier,” he said. “Of course anything that’s fully adhered is going to be tighter. A house wrap is going to leak more than a liquid-applied system like a Cat 5 or a self-adhered membrane. If it’s fully adhered to the sheathing, you’re going to have a better level of success.”
Jones has witnessed very few failed blower door tests in his career, but he's never surprised at the ones that fail because they all have one thing in common.
It’s evident that the contractor just doesn’t care.
“You can tell they’re not putting in the effort to do their own QC,” Jones said. “They’re doing things sloppily, they don’t see the value in it, and you can kind of just tell based on their attitude toward it. We’ve never walked into a test that failed miserably and we’re scratching our heads.”
RDH Building Science has offices in Vancouver, Victoria, Courtenay, Toronto, Portland, Waterloo, Seattle, San Francisco and Boston. To learn more about Denali Jones, RDH Building Science and what advantages they bring to project teams, visit RDH.com.