In existing masonry construction, the connection between masonry veneers and the back-up materials can be compromised over time. Mechanical retrofit anchors are designed to functionally replicate wall ties that were either inadequately installed, corroded, or insufficient in number.
Tech Note 104
Compiled April 2021
Author(s)
Steve Getz
Sarah Holder
Alley Mathson
Jeff Scarpelli
Location
3741 Greenway Circle
Lawrence, KS 66046
Contact
prosoco.com
800-255-4255
customercare@prosoco.com
Introduction
In existing masonry construction, the connection between masonry veneers and the back-up materials can be compromised over time. Mechanical retrofit anchors are designed to functionally replicate wall ties that were either inadequately installed, corroded, or insufficient in number. Restoring anchorage involves balancing performance requirements with installation methods and long-term durability. When optimized, these functions produce effective retrofit anchors for use in existing masonry construction.
Mechanical Anchors
Mechanical anchors provide a high strength connection intended to reconnect an exterior masonry veneer to various back-up materials. When installed, the post-installed expansion anchors grip the two existing walls. The anchorage is comprised of two independent anchors, one in each wythe. They are connected but do not draw the two walls together. The connection materials must be sufficiently stiff to transfer wind-induced forces (both inward and outward) between the outer envelope material to the internal building structure. Activation of the anchor is torque induced to measurably determine an effective grip.
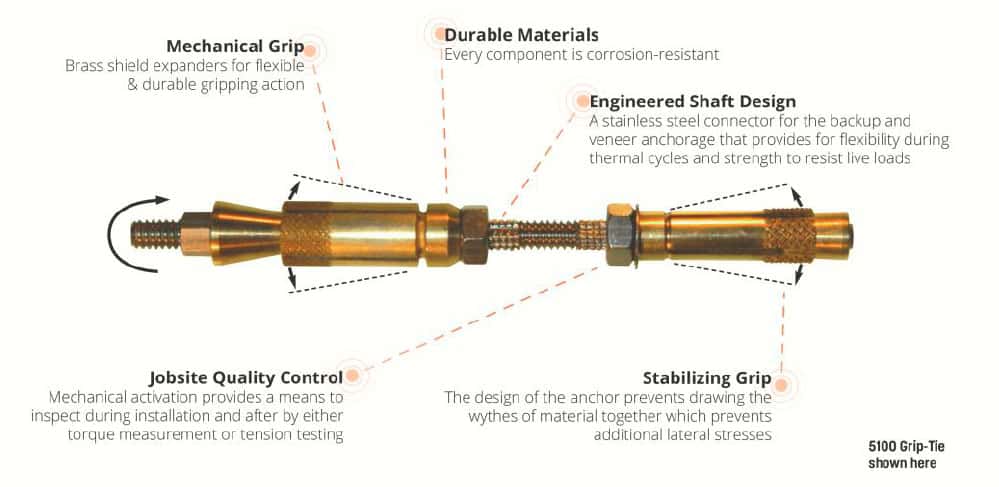

Download this Tech Note as a PDF
The manufacturing material must be durable, strong, and corrosion-resistant. The resulting anchor design utilizes brass expansion elements and stainless-steel connection hardware. The brass is sympathetic to the masonry material, ductile, cost-effective, and corrosion-resistant. The stainless-steel components strategically satisfy the functional characteristics and corrosion resistance of the retrofit anchor assembly. Discussions regarding the combination of dissimilar materials, such as stainless steel and brass, and their corrosion potential are common. The following information is intended to provide a description of the mechanisms of galvanic corrosion and explain whether there is potential for galvanic activity in the two material combinations.
Galvanic Corrosion
The concept of galvanic action (voltage) can be traced to the 1800s when the first “battery” was developed by Alessandro Volta. This battery was created by stacking sheets of copper and zinc plates separated by brine-soaked paper. The combination of dissimilar metals and the incorporation of an electrolyte (the ion enriched, saltwater solution) induced galvanic corrosion, which resulted in measurable voltage. In this experiment, the copper, a more noble metal, acted as the cathode in the reaction, while zinc, a less noble metal, became the anode and corroded preferentially. The electric current (galvanic action) developed between the materials created galvanic corrosion.
For galvanic corrosion to occur, these conditions must be met:
1. Two dissimilar metals must be in direct or close contact.
2. A large difference in galvanic potential must exist. (outlined below)
3. And a conductive electrolyte such as ion-influenced water must be present.
Metal Influence
In metals, corrosion is the reaction of a metal to its surrounding environment. The corrosion potential is determined by the type of metal and the environment in which it is placed. When different metals are combined and subjected to the same environment, corrosion will occur at different rates. If both metals are then placed in a different environment, their corrosion rates may be influenced disproportionately. In terms of galvanic corrosion, metals are considered dissimilar when there is a large difference in galvanic potential.
The galvanic potential is directly linked to the order of nobility for each metal. They are listed in the galvanic series from those that are least active, or noble (cathodic) to those that are the more active (anodic). When the conditions for galvanic corrosion are met, the less noble (active/anodic) metal will corrode preferentially and be consumed. The closer the metals are in the galvanic series, the more resistant they are to galvanic corrosion.
The abbreviated list on the left is taken from a longer table within the Army Missile Command Report RS-TR-67-11, "Practical Galvanic Series.” The metals are listed in the order of their reactivity in a seawater environment. The order of the galvanic series is subject to change dependent on the environment or electrolyte present.
Electrolyte
Electrolytes are an important component in galvanic corrosion as their presence causes the reaction between dissimilar metals. The composition of electrolytes can be acids, bases, and/or salts. When an electrolyte is dissolved in water and undergoes ionization, the solution becomes a nonmetallic electric conductor. In concept, rainwater should have little to no ionization. However, due to industrialization, rainwater today is acidic and can be considered a good electrolyte. In high exposure areas, rainwater can influence galvanic activity. The positioning of mechanical anchors within the wall assembly allows for limited, intermittent exposure to an electrolyte. Without the constant presence of an electrolyte, the potential for galvanic activity is minimized.
Surface Area
In addition to the influence of an electrolyte, the rate at which galvanic activity occurs will vary with the ratio of areas between the dissimilar metals, also known as the “area effect”. If the cathodic metal has more surface area compared to the metal acting as an anode, there is a greater potential for the galvanic activity to occur. If the ratio is flipped, and the anodic metal has more surface area than the cathode, there is less potential for the galvanic activity to occur. At an area ratio of close to 1:1 between the brass and stainless-steel components, the potential for galvanic activity due to the area effect is minimal.
In some cases, surface conditioning, such as applying finishes or plating is utilized to prevent galvanic corrosion. The potential for significant galvanic corrosion between brass and stainless-steel (type 304/316) components is minimal, so this type of abatement would not produce a measurable benefit.
Metal Voltage
Assuming two of the three conditions are met for galvanic potential, the severity of the galvanic corrosion relates to the metals’ potential to react. The electrical voltage difference of metals provides a guideline for the use of dissimilar metals. The electromotive force series ranks metals as to their inherent reactivity.
The metals located at the top of the series are considered the most noble, whereas metals that can be found at the bottom are the least noble. This series helps determine the tendency of a metal to release energy and corrode. Applying this resource allows one to evaluate the possible exposure concerns. The list to the right is a simplified version of the NASA and military standard – NASA-STD-6012.
This standard outlines the acceptable differences in voltage for dissimilar metals related to the environmental conditions:
a) Harsh environments: 0.15 V difference or less
b) Normal environments: 0.25 V difference or less
c) Controlled environments: 0.50 V difference or less
In this instance, the use of Brass (0.40 volts) and 18% Chromium type stainless steel (0.50 volts) creates a voltage difference of 0.10 V. This falls below the recommendation for Harsh environments (0.15 V difference or less) and significantly below the recommendation for normal environmental exposures (0.25 V difference or less).
CONCLUSION
In the case of mechanical anchors where brass and stainless-steel components are used, the potential for galvanic corrosion is greatly reduced due to: their proximity in the galvanic series, the intermittent exposure to an electrolyte, and the 1:1 cathode to anode surface area ratio. Finally, according to NASA-STC-6012, the voltage difference between the brass and stainless-steel components used will result in minimal galvanic activity in both normal and harsh environments.
REFERENCES
AMPP: Association of Materials Protection and Performance. n.d. “Galvanic Corrosion.” Accessed February 23, 2021. https://www.nace.org/resources/general-resources/corrosion-basics/group-1/galvanic-corrosion.
NASA Technical Standards System. 2012. “NASA-STD-6012 Corrosion Protection for Space Flight Hardware.” Accessed March 11, 2021. https://standards.nasa.gov/standard/nasa/nasa-std-6012.
Specialty Steel Industry of North America. n.d. “Galvanic Corrosion.” Accessed April 9, 2021. https://www.ssina.com/education/corrosion/galvanic-corrosion/.
United States Army Missile Command. 1967. “Report No. RS-TR-67-11 Practical Galvanic Series.” Accessed April 8, 2021. https://apps.dtic.mil/dtic/tr/fulltext/u2/823185.pdf.