As discussed in our recent post about quantifying structural air leakage through the use of a blower door test, this process is crucial to preserving indoor air quality (IAQ) and avoiding issues like mold, static electricity and energy waste.
Having established the “why,” let’s turn now to the “how.” Jake Bruton, owner of Aarow Building outlines the process step-by-step below.

Need a blower door test for commercial construction?
1. Confirm that all open-flame areas are extinguished and dampers are closed. This includes fireplaces, wood stoves and the like. You may even want to cover fireplace ashes with wet newspapers to prevent them from being sucked around the house during the test.
2. Create an airflow path. This applies to all conditioned spaces — in other words, those that are cooled or heated, either directly by HVAC equipment or indirectly by their proximity to adjacent spaces. Close and lock all windows and doors, except for the one to be used by the test. Interior doors must be left open. Open the hatch on any crawl space if it’s considered part of the conditioned space; otherwise, leave it closed.
3. Turn off any gas appliances. This includes water heaters and commercial stove pilot lights. Because the house will be depressurized during the test, these appliances would present dangers such as back drafting and gas fume infusion if left on. Turn off any electric appliances, along with HVAC, bath fans, or other ventilation devices.
4. Mount the blower door into one of the exterior openings. The blower door includes a powerful fan to pull air out of the building, thereby lowering indoor pressure and forcing the higher-pressure outdoor air to come in through any unsealed openings. It also includes a device for measuring airflow, known as a manometer. Follow the manufacturer's recommendations for fan orientation and manometer setup.
5 .Take an outdoor pressure reading. This reading will be plugged into the manometer to serve as a reference for the negative pressure to be created during the test.
6. Turn on the fan and run the test. The manometer will calculate the amount of leakage, expressed as the number of air exchanges per hour.
7. Inspect for leaks. The manometer reading is only one of the items to consider; it’s also important to walk around while the fan is still running and take note of any leaks that can be heard or felt.
8. Make repairs. For new construction, it makes sense following the test to fix any leaks and then to re-perform the procedure. For existing construction, make recommendations for repairs that can be completed later.
9. Re-perform the test at a higher pressure differential. Regardless of when repairs will be made, turn up the pressure and repeat the test. More leaks will often be revealed during this type of second pass.
10. Return the building to pre-test conditions. This includes reigniting water heaters and gas stoves and cleaning up any debris.
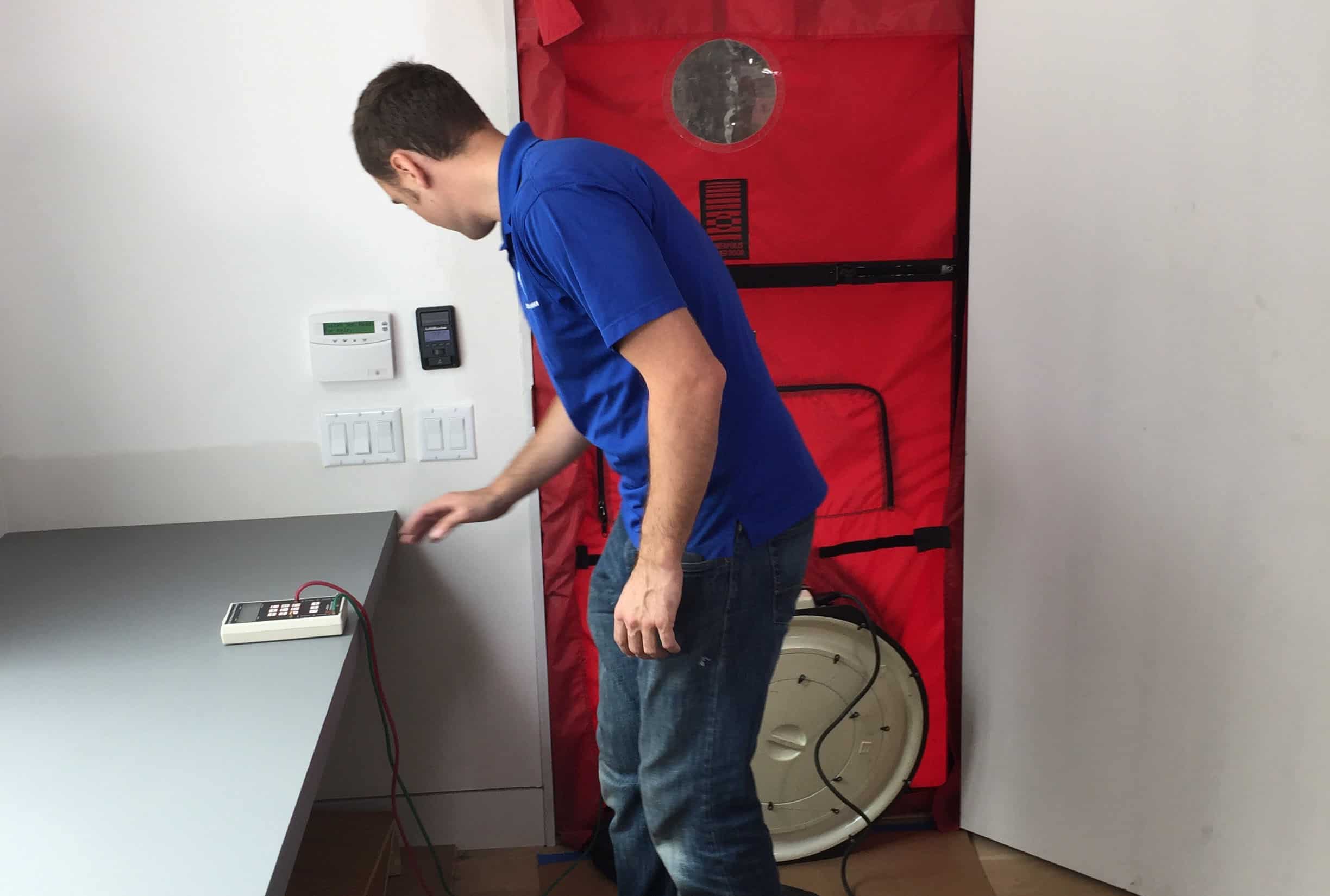
For the test to be effective, as Sean Harris pointed out in our previous article, the pressure difference between inside and out must be a minimum of 50 pascals. This is a small fraction of the pressure in a car tire: just 1 psi is equivalent to nearly 7,000 pascals. But the difference is enough to simulate a 20-mph wind on all sides of the building, equalizing the space and revealing its defects.
In real life, of course, pressures are more dynamic. Simply opening and closing an exterior door can cause air to move in and out of holes in the building envelope — the physical separator between the conditioned and unconditioned spaces of a building. During the heating season, warm air rising within a building decreases pressure at the base that draws in cold air; this is known as the stack effect, and it can cause heat to escape through openings at the top. Indoor-to-outdoor temperature differences also encourage air to move from side to side in an attempt to achieve equilibrium. In addition, air movement caused by mechanical fans — including those in HVAC systems, range hoods, dryer vents and bath vents — can similarly wreak havoc.
All of these dynamics underscore the importance of an ongoing focus on the building envelope. Performing blower door tests at multiple stages of construction offers a great deal of actionable data; waiting until the final stages to find deficiencies makes it far more difficult to correct them. By taking the long view and incorporating sound practices throughout the process, you can ensure durability and resilience.